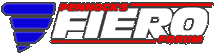

 |
Trinten's SBC/F23 build - The work has begun! (Page 58/74) |
|
La fiera
|
FEB 02, 07:20 PM
|
|
That's some nice work Vince! Is he going to build a support/bracket to hold the turbo in place to take the weight/load off the exhaust pipes?
|
|
|
Trinten
|
FEB 02, 08:46 PM
|
|
There is already a support system in place, it's also where the turbo drain is tied in. If you look at the first picture from my post on Jan. 25th, you can see just a hint of the black tube going up on an angle under the turbo. That's one of the support legs.
It's been mounted for a while, when the engine was in the car still. Here's an earlier pic where you can see the turbo 'floating', it's just obscuring it's legs. They run down and bolt to the transmission housing.
|
|
|
Will
|
FEB 03, 11:51 AM
|
|
Have you checked out PMBrunelle's turbo support? He took a page straight out of Formula 1's first turbo era...
https://www.fiero.nl/forum/...ML/142133-2.html#p48
quote | Originally posted by pmbrunelle:
Here the turbo support is installed. Its function is to support the weight of the turbo, to take the weight off the crossover pipe.
I'm using a RH-LH pair of 7/16"-20 rod ends threaded into a hex rod. Since the crossover pipe sags by 0.008" under the weight of the turbo, I simply crank up the rod-end assembly to raise the turbo's position by 0.008". The idea is to put the crossover pipe into its "zero-stress" position.
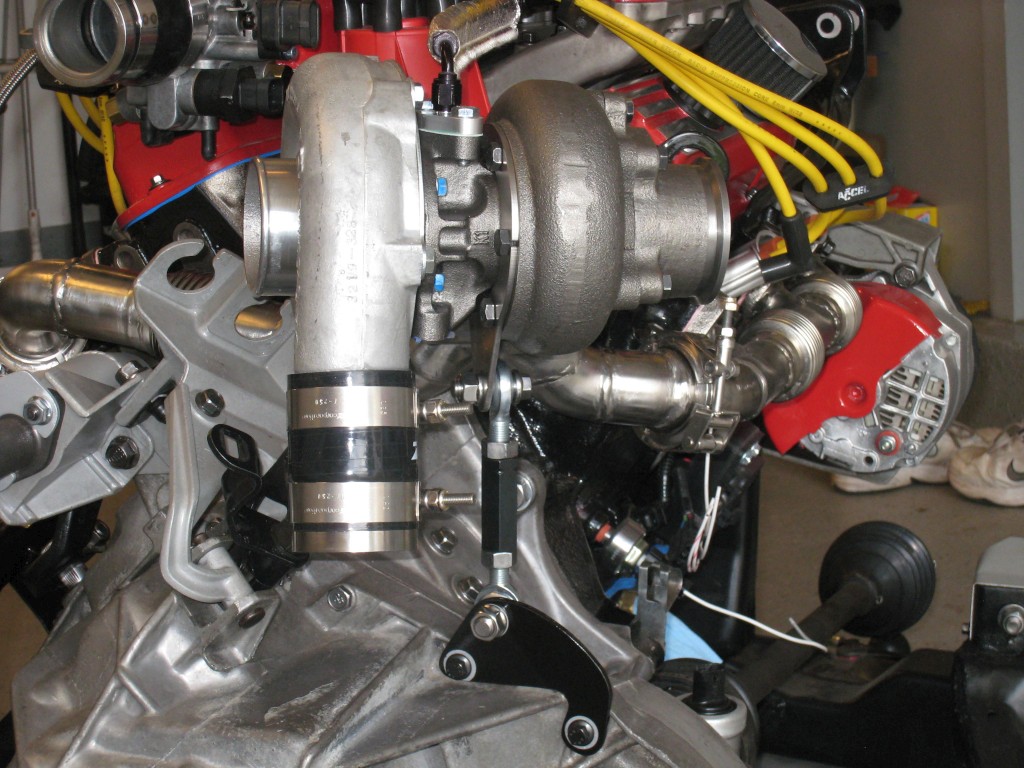
I was inspired by seeing many 80s turbo Formula 1 engines having this kind of setup.
Honda RA166E: https://upload.wikimedia.or..._Collection_Hall.jpg Renault EF4: https://upload.wikimedia.or...n_Player_Special.jpg TAG-Porsche: https://upload.wikimedia.or...t_Porsche_Museum.jpg
However, it's not because this design is found on race cars that it's suitable for a street car. I guess I'll see what happens. |
|
|
|
|
Trinten
|
FEB 03, 02:42 PM
|
|
That's a pretty neat idea. Mike figured out placement and made the turbo mount before he started finalizing any of the "Duct work", so the weight of the turbo won't pull down on anything. Pmbrunelle's setup is definitely more polished than what we came up with. We used chrome moly tubing, cut off a piece to turn 90 degrees, welded to the 'leg' (cutting an arc into the leg so it fit flush with the 'foot'), welded on a cap to the 'foot', drilled through the cap for the bolt hole. So the feet line up with the two bolts on the transmission, and the bolt goes through the open end of the foot. ...
I hope that made sense. When the turbo is mounted again, I'll take pictures of it.
|
|
|
Will
|
FEB 03, 02:52 PM
|
|
Things that change in temperature by 1000 degrees during operation are going to move around due to thermal expansion... That's why F1 teams started with the flexible turbo supports... so that they wouldn't be imparting stresses to the hot header tubes because of a rigid turbo support. Food for thought.
|
|
|
Trinten
|
FEB 16, 12:14 AM
|
|
When temperatures have cooperated, Mike has been busy with mocking up, measuring, and (re)modifying the exhaust plans. Still a lot left to weld, but he is happy with the progress so far, and is trying to take into account spacing, serviceability, hoses, wiring, and of course thermal control.
He's very focused on the details. At one point he had another piece welded into place, and it was not quite parallel to the cross member of the cradle. And I mean, I didn't see it until he busted out a measuring tape, but he saw it without that. So I asked:
"Is that going to cause a problem?" "Yeah." he replied "What?" "It's going to annoy me." was his answer. So he then went about fixing it.
He had been sending me pictures of his different mock-ups, but I wanted to wait because I knew things would change. You can see in one of the pictures all of the magic marker "line-up" marks from the current and previous fits. 
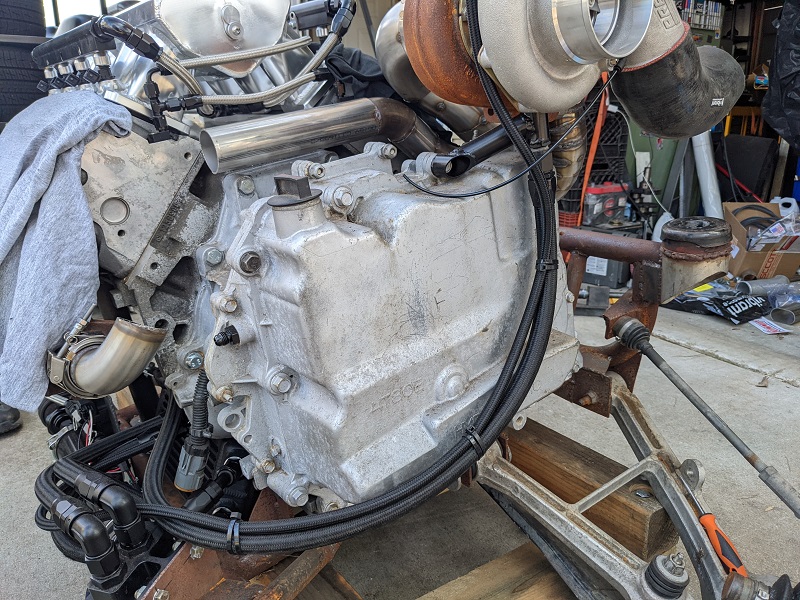
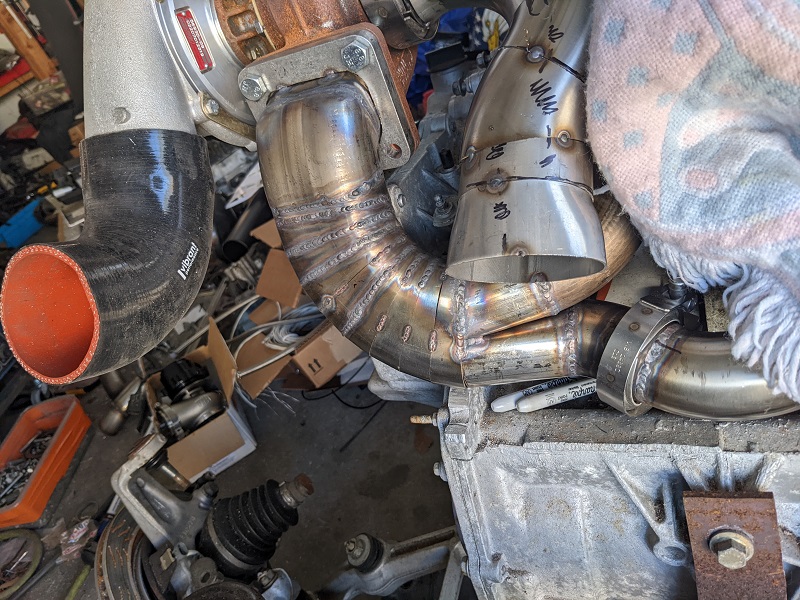
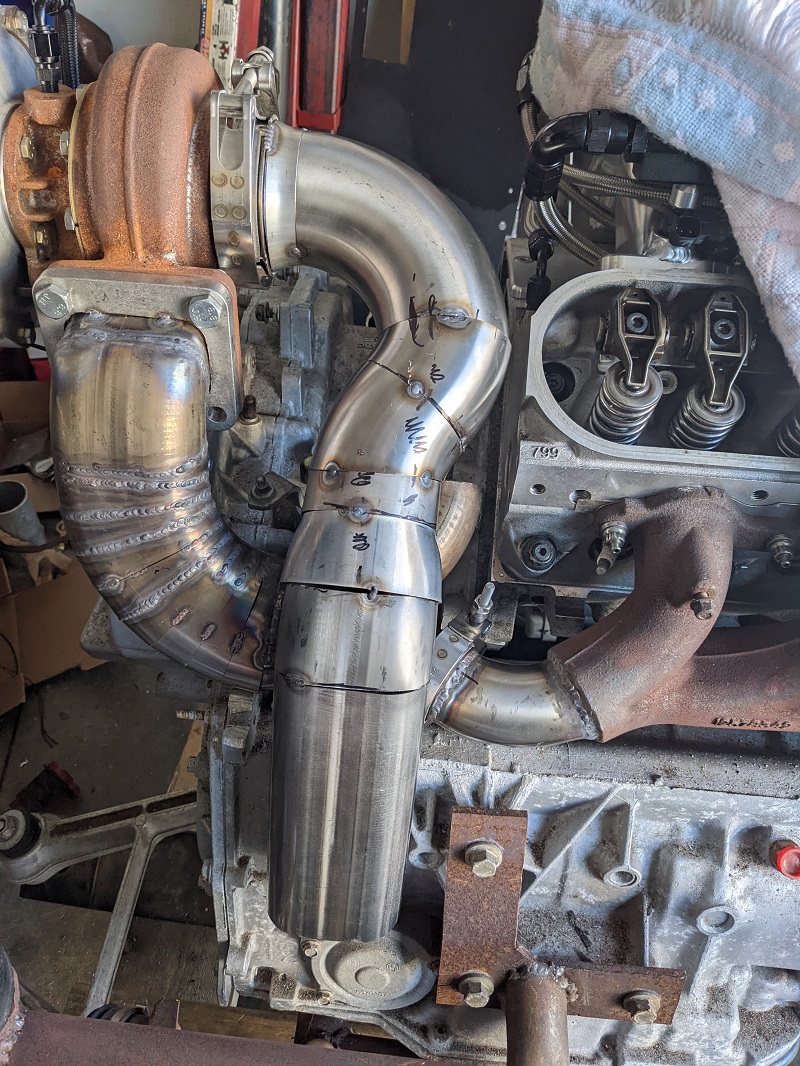
I'll hold off on talking more about the plans for the exhaust until they come to fruition. That way I have something to go with the pictures.
The next wave of things came back from powdercoating!
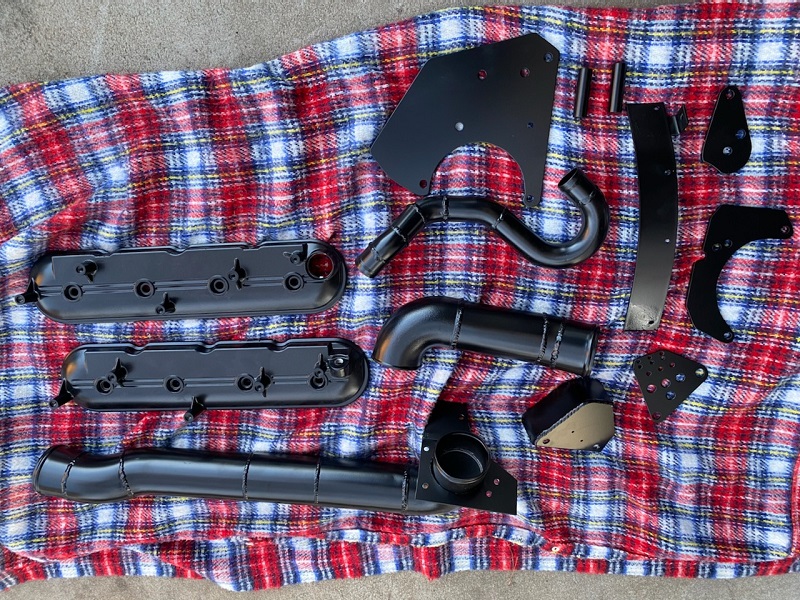
That is all of the current brackets to fit the accessories and such to the engine, plus the valve covers, of course. I wanted a few of them done in silver as accent pieces, but the powdercoating guy was being a bit of a jerk to Mike over the pricing (almost doubling the price, even though everything would go in the oven at the same time). Mike made an executive decision to just do it all in black.
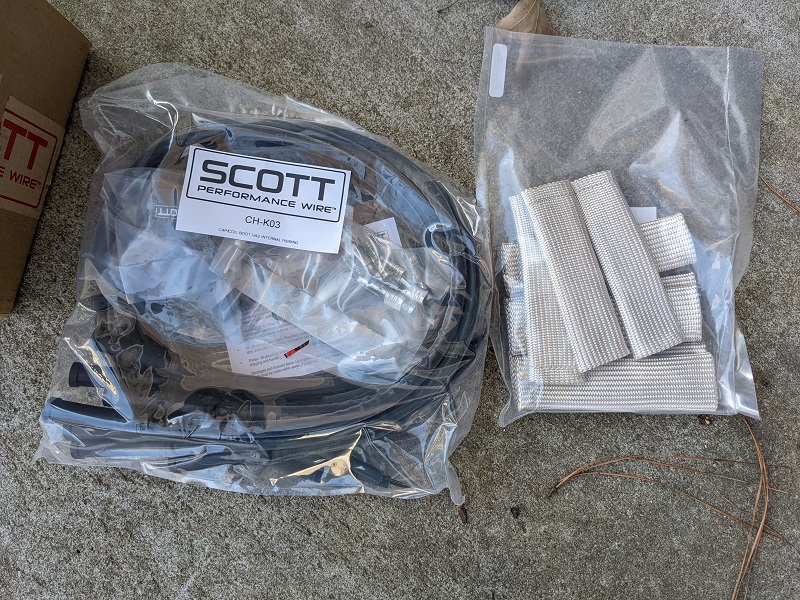
I also had a heck of a time getting the Taylor wires I wanted. TWO orders from two different vendors who said they had them in stock cancelled the order because "Oops, by in stock, we really meant they'll ship from the manufacturer, and they don't have any...."
So after much Googling and reading up on wires used by other guys putting down big enough power that they were having spark issues with OEM wires, I found Scott Performance wires, right here in N.C. Apparently they also make wiring sets for stock car teams?
I called and spoke to them, explained what I wanted, and they were really great about it. Gave me a quote, and I received the wires on time. Mike said that visually they look good, they have a double sleeve, plus I got the thermal socks for them.
And since we are now waiting on more material to come in to do the exhaust, Mike switched gears to wiring for the moment. He started breaking down the stock harness and fitting it, taking out things we don't need. This will become our prototype wiring harness to run and do testing with. And then it will go in a box as an emergency backup.
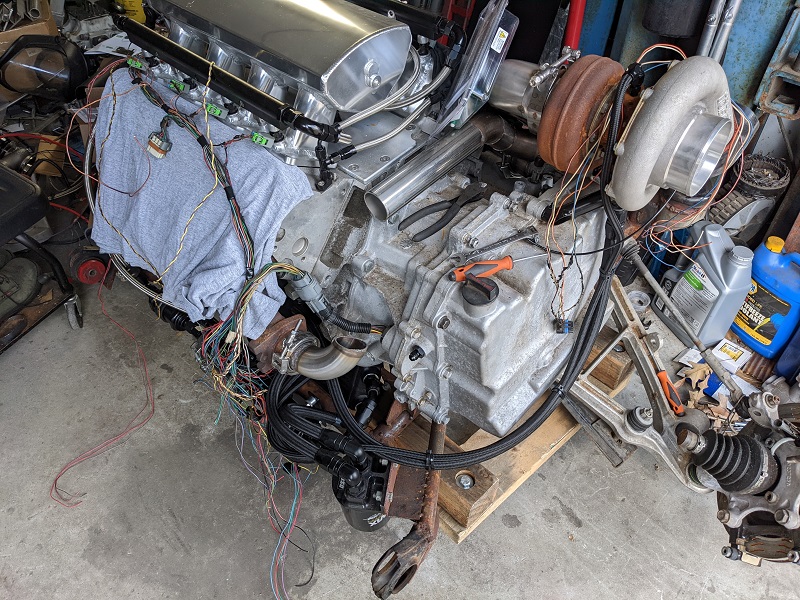
Once that is done and all is working, the prototype harness will come out and we'll be using all that wire I bought to make a new engine harness, along with all the spiffy various-degrees-of-shielding loom. I learned about https://lswiring.com/ from reaching out to EFIConnection (they own LSwiring.com as well?). I wanted to find an easy source to get bare connectors. They have a nice system were you can search by engine and it'll give a list of all the connectors they have for it.
We did find the pushrod length measuring tool. We marked the top (nose?) of the valves, and he put a breaker bar on the crankshaft to rotate the engine assembly a few times to see where the marking would be rubbed off by the tappets. Stock LS4 pushrods are 7.4", the ones I have arriving are 7.475".
[This message has been edited by Trinten (edited 03-26-2023).]
|
|
|
Trinten
|
FEB 21, 02:40 AM
|
|
So some of the exhaust materials that Mike needed were coming from a place in Washington state, so unfortunately it didn't reach him by the weekend. Other parts were coming from Summit and one piece of 0.064" t-6061 aluminum from Amazon. With the stuff that did show up, he was able to mock up one more part of the exhaust. The downpipe and the rest needs to wait until the rest shows up this week.
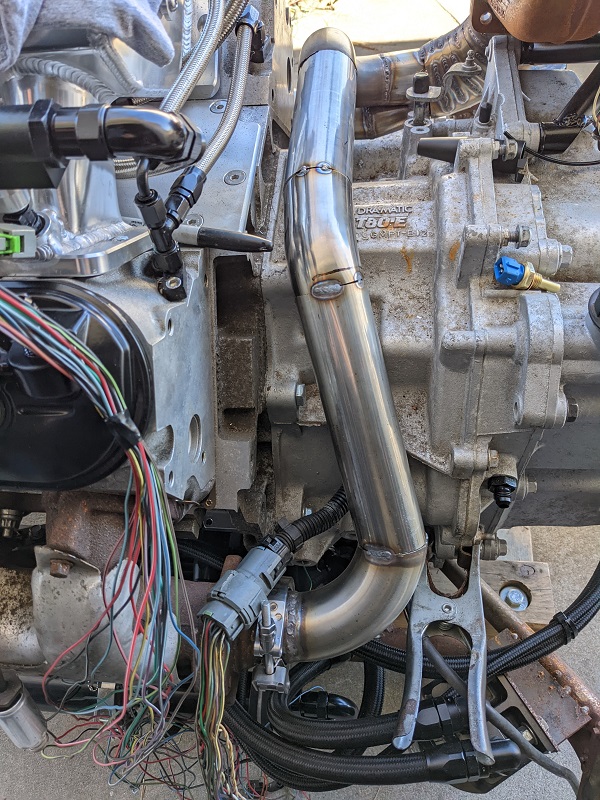
With what did show up, we were able to make the single piece shims. Mike cut them to fit the rocker stand. The holes were chamfered. When those were installed and pushrods put in, he marked the nose of the valve and rotated the engine to make sure all the geometry landed where he wanted it, and it did.
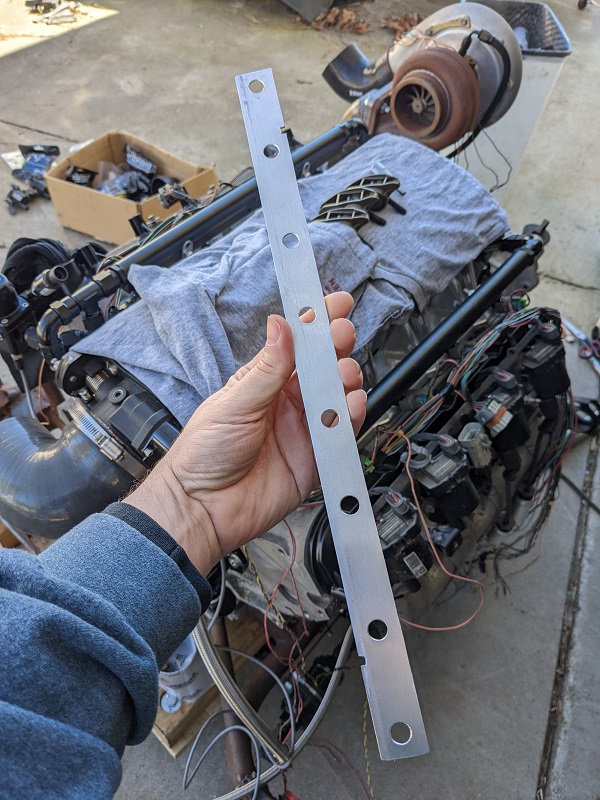
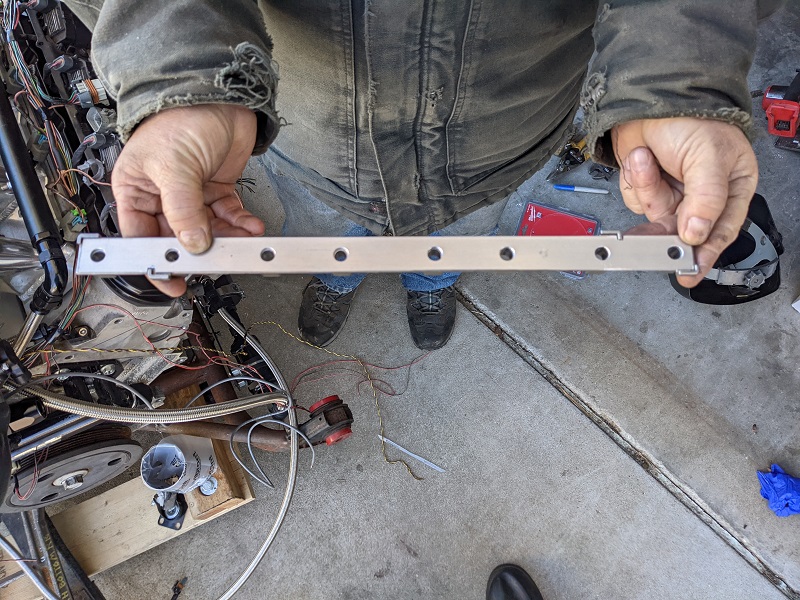
You can see the powdercoated parts were also on. The big bolts for all of the accessories were figured out a while back, with washers so the powdercoating can't be dug/twisted when we torqued down the bolts.
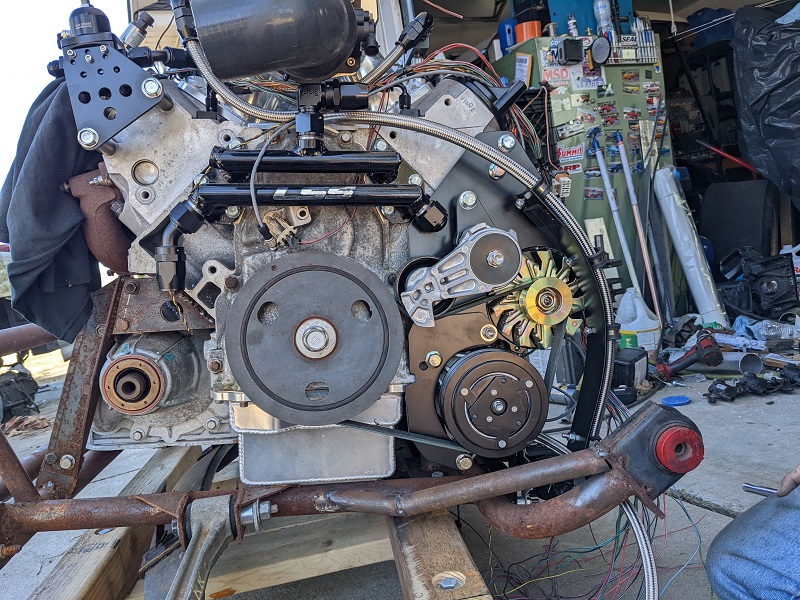
The local Ace Hardware did not have the stainless hardware we wanted for all the p-clamps for the hose and other things, so McMaster-Carr has an order from me for screws, nuts, and washers.
Here is a shot of under the intake where we started plumbing in hardware. The vacuum tube will be using a length of hard tube that will extend out just a little past the intake, and the hose will fit to it there.
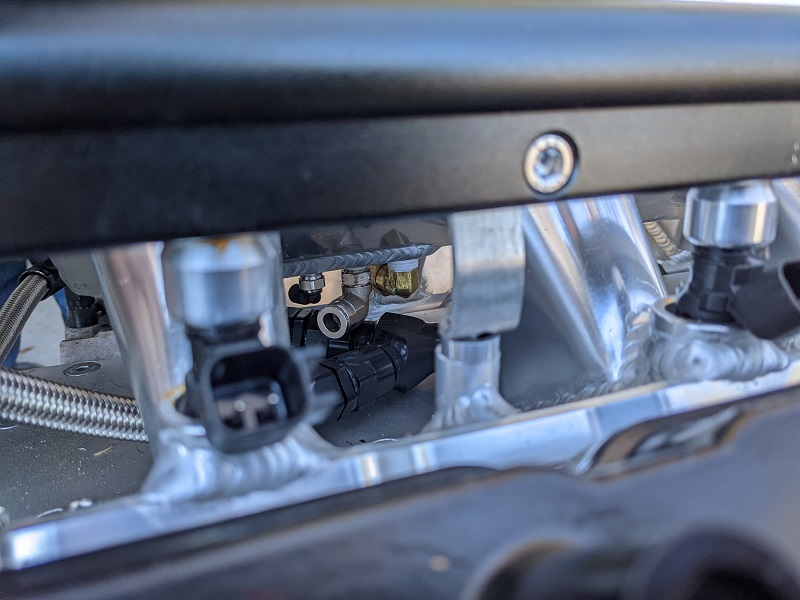
Mike really wants to get the exhaust done by the end of next weekend, so I can take that to Jet Hot, and he can take the drivetrain off the cradle to finish the welding on that, and then it goes off for powdercoating.
[This message has been edited by Trinten (edited 03-26-2023).]
|
|
|
Trinten
|
FEB 27, 05:35 PM
|
|
Yesterday was 99% watching Mike measure, cut, spot weld, repeat!
I did a little work, replacing some of the p-clamp fasteners with 316 stainless ones, but that's boring stuff, and you guys are here for the cool stuff!
One of the things I failed to find was a smooth transition 90 degree Y-pipe, that was 3" and dual 2.5" out. I could find them in aluminum all day long, but since the exhaust, save for the manifolds, is all stainless, I wanted tobe consistent.
Magnaflow made one, but it's in 409 stainless, which is apparently lousy. So Mike had me get him two 2.5" tight radius 90s in 304, and he made the Y pipe that he wanted.
He said it was a little tricky, since stainless doesn't have the ductability that aluminum does, so you need to be careful about how much you bend it and where, or else it'll either fail right then, or fail in the future (especially with exhaust stuff, if it's close to the manifolds, or is the manifolds!)
Here are some shots as Mike made the Y-pipe, clamping, squishing, checking, etc. I only took a few pics, but this was a time consuming project.
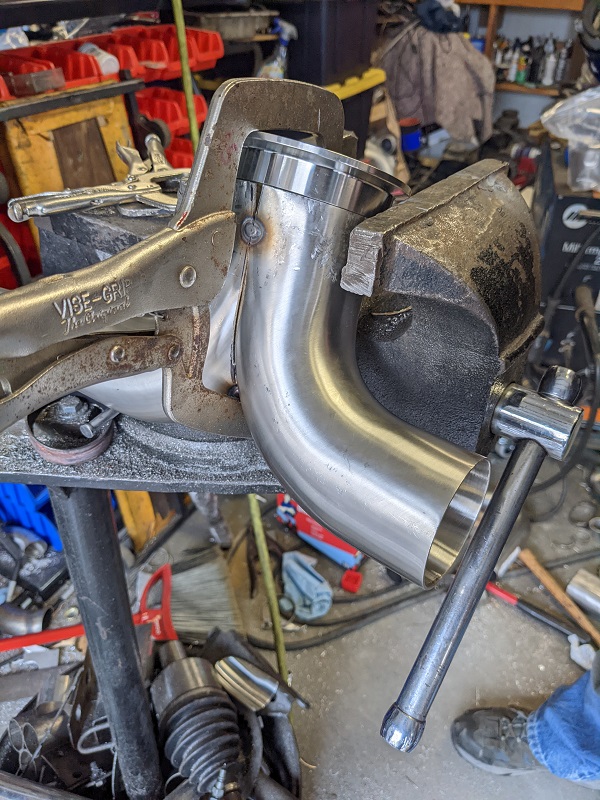
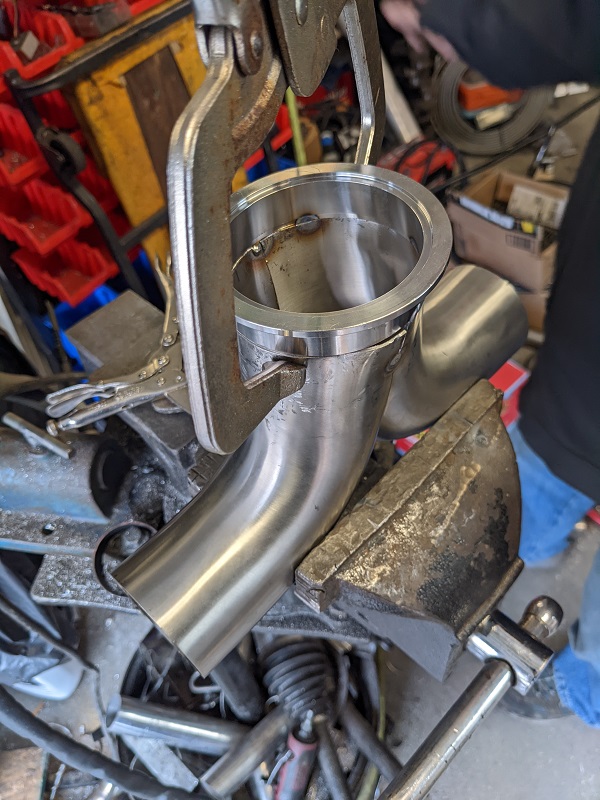
Then once the Y was spot welded, we did some test fits and measurements. We found with the muffler I picked, we had to extend the downpipe out a little more.
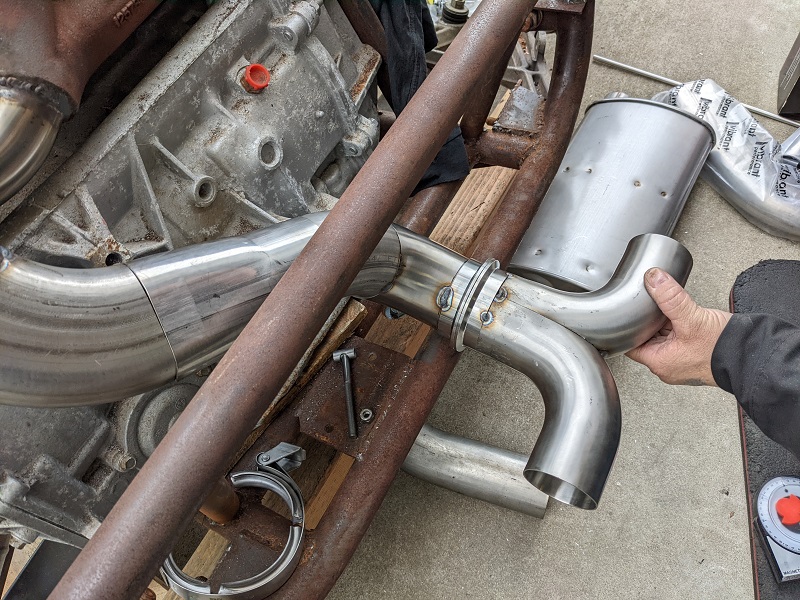
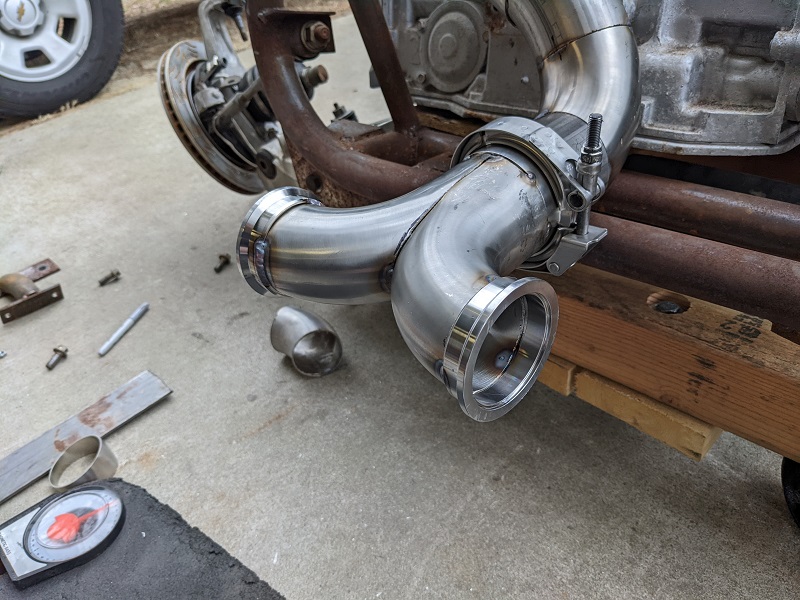
After the downpipe was modified again, we put the v-band on the Y and test fit the mufflers
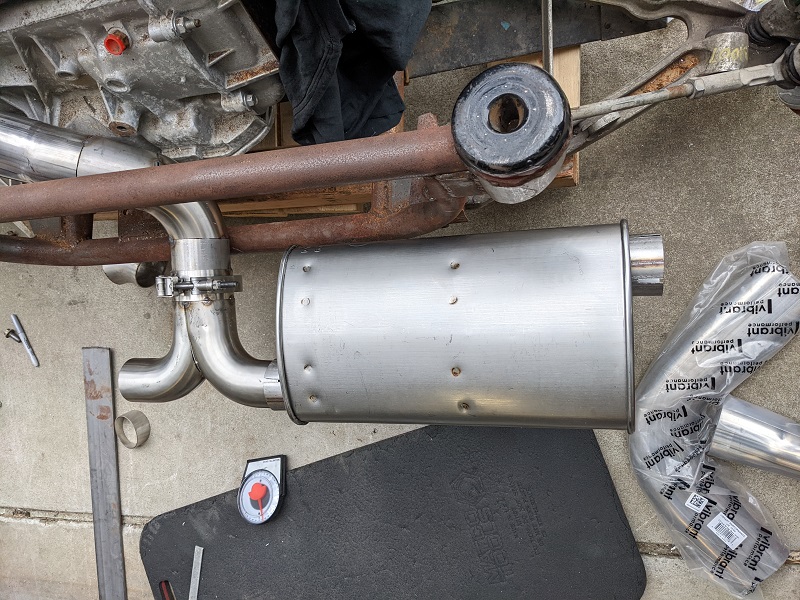
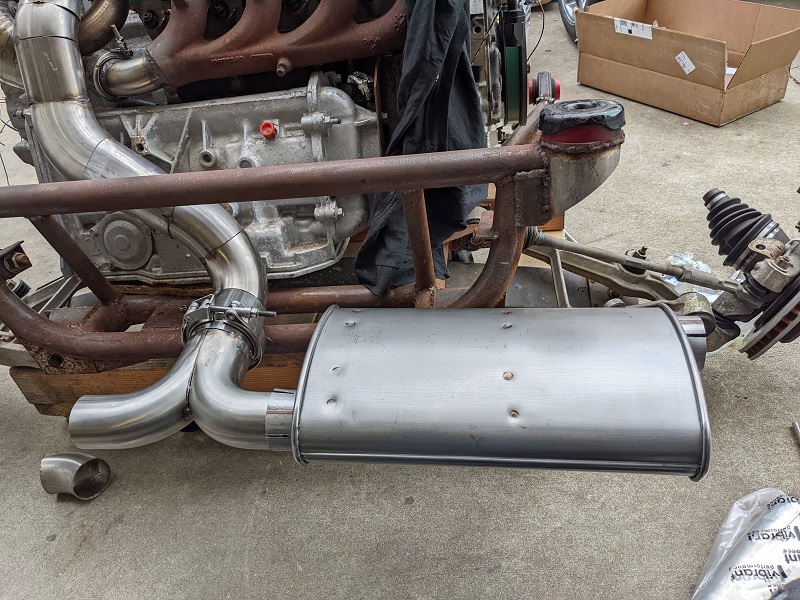
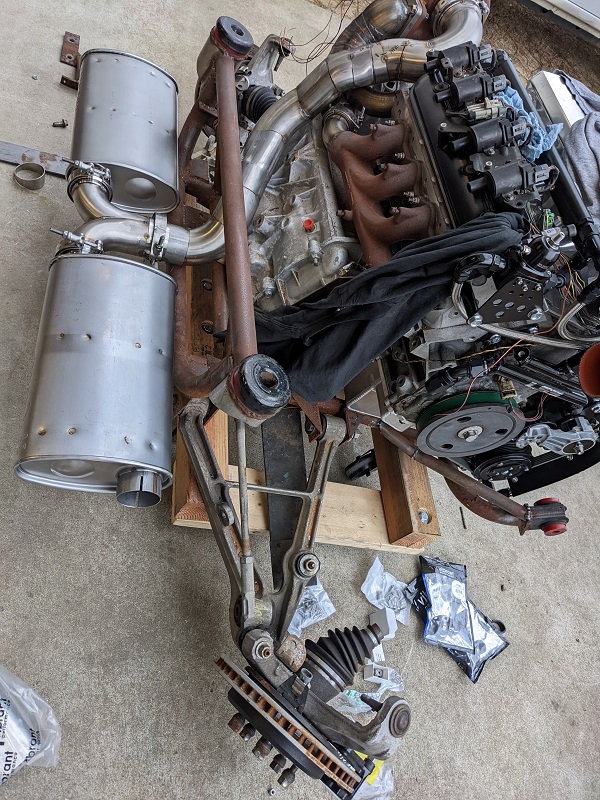
The mufflers will also be modified for V bands as well. This way it'll be easy in the future to make adjustments, I can pop off the mufflers easily, either for the track or for other mufflers. And the downpipe can be lengthened/shortened now too (if future muffler selection demands it), only requring another v band to be welded on.
This way I can try to find mufflers that will keep the car quiet enough for me to enjoy, but not strangle the engine, and hopefully not anger my neighbors.
Everything will be hung/mounted from the cradle, making it an easy package to drop out once all hoses/wiring is disconnected.
Mike estimated another 10 hours to do the finish welding on all of the exhaust now. Once that's done, that'll be off to Jet Hot, engine and transmission will be put on stands, cradle will be finished welding and off to powdercoating.
[This message has been edited by Trinten (edited 03-26-2023).]
|
|
|
Will
|
FEB 28, 11:39 AM
|
|
quote | Originally posted by Trinten:
So some of the exhaust materials that Mike needed were coming from a place in Washington state,
|
|
Sounds like Columbia River Mandrel Bending
|
|
|
Trinten
|
FEB 28, 12:08 PM
|
|
quote | Originally posted by Will:
Sounds like Columbia River Mandrel Bending  |
|
The store was Ace Race Parts. I don't know if they are partnered with Columbia River Mandrel Bending
|
|

 |
|