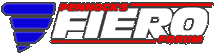

 |
Basic Fiero electrical testing "How To" and equipment...with pics. (Page 1/4) |
|
fierohoho
|
MAR 17, 12:44 PM
|
|
I have seen quite a few new Fiero owners here over the years who have needed help with doing some basic trouble shooting and repairs on the Fiero electrical system, which as we all know can be troublesome at times.
What I offer here is a basic description of the types of tools available, how to use them and some wiring repair.
I welcome any other advice to help clarify things for the Fiero owners who are learning to repair their cars themselves or if you have any tips.
I plan to start this with what I think are the basics.
In my opinion a basic set of electrical tools need not be expensive and are fairly easy to aquire whether you go to Radio Shack a home improvement center or an auto parts store.
Lets start with the tools.
A Multi Meter, either digital or analog.
They come with two test leads, a red and a black and they usually run on a regular household battery.
This is a digital Multi Meter, I recommend this type.

This is an analog Multi Meter, it does the same thing but the needle can bounce around if bumped.

A small set of test leads.

A 12 volt test light.

A wire cutter and a wire stripper, more on the wire strippers later.

Another type of wire stripper also used with crimp connectors, more on those later.

Soldering irons.
A Weller brand "gun" type which I prefer as it heats when you pull the trigger and cools off fairly quickly when you release the trigger, it even has a small light that shines on the work when the trigger is pulled.

A Weller brand "pencil" type, this you plug in, it heats up and is always hot, works ok and burns you even better if you're not careful.

------------------
 Where will the road take you today?
Some helpful links I've done How to remove inner door panels, with pics. How to remove outer door panels, with pics. How to make rear coil-overs using factory struts, with pics. How to remove rear bearing hubs, with pics. How to modify the stock Fiero radio for MP3 players, with pics. How to come up with the right coolant hoses for that engine swap...With Pics. Basic Fiero electrical testing "How To" and equipment...with pics.[This message has been edited by fierohoho (edited 04-02-2007).]
|
|
|
fierohoho
|
MAR 17, 12:52 PM
|
|
|
|
Bruno Mid Engine
|
MAR 17, 01:00 PM
|
|
Man, this is worth one of those + things for you. L8R Bruno
|
|
|
fierohoho
|
MAR 17, 01:11 PM
|
|
|
|
fierohoho
|
MAR 17, 01:24 PM
|
|
|
|
fierohoho
|
MAR 17, 01:35 PM
|
|
|
|
fierohoho
|
MAR 17, 01:43 PM
|
|
Now a little on heat shrink tubing. I use it exclusively when I splice a wire as it seals the wire much better against the elements than a crimp connector and electrical tape.
The biggest thing to remember is to put it over the wire "BEFORE" you solder the splice. You have no idea how many times I've had to cut a splice apart just to add the heat shrink tubing because I forgot. It's also important to size the heat shrink tubing to the wire you're working on, too big and a poor seal, too small and it may not fit over the splice.
Here's a small piece of tubing before it was heated.

Here's the same piece after I heated one end of it. You can see how much it shrinks down and that is what keeps the splice clean and dry.
 [This message has been edited by fierohoho (edited 12-01-2008).]
|
|
|
fierohoho
|
MAR 17, 01:59 PM
|
|
|
|
fierohoho
|
MAR 17, 02:25 PM
|
|
OK, now lets solder two wire together.
One tip I have is that when you solder wires you will almost always have a few drops of molten solder fall from the wire, place an old mat or a piece of cardboard under the work to protect whatever is underneath.
Start by stripping the ends of the two wires about 3/8" to 1/2", if you're going to seal the connection with heat shrink tubing slide it over one of the wires now.
I then twist them together parallel. Make sure the ends lay flat against the wire so nothing can poke through whatever you cover the joint with and cause a shorting condition.

The key to a good solder joint is in the wire being clean and shiney, if you have a wire that is a little tarnished you can clean it up using a piece of sand paper, steel wool, a scotch brite pad, anything to make the wire shiney.
Once the wires are clean and twisted together it's time to heat them with the soldering tip. Place the hot tip on the wires and let it heat them a few seconds, then touch the end of the solder to the wire and tip, when it starts to melt the solder, lightly move the tip across the wire joint to help spread the solder along the joint, the solder will "flow" onto the wire when hot enough.

When it looks like the joint is covered it will be silver in color, you can stop and let it cool. There will be a little smoke when you do this, that's from the rosin core in the solder, this rosin core helps clean the wire a little more and it helps the solder to flow onto the wire.

When the connection has cooled so you can touch it with your fingers and not get burned slide the heat shrink tubing over the splice.

Now heat it with a match or lighter and shrink it down, as you heat it move the flame back and forth along the tubing, it will shrink one side more than the other so also rotate the wire as you do this. That's it, you're done.

Here are two pics I found on the web of a neat and easy to build extra pair of hands for holding two wires you're going to solder.


There you are folks, the basics, fierohoho style.
Please feel free to add to this to help those that need it.
Steve[This message has been edited by fierohoho (edited 03-17-2007).]
|
|
|
partsman
|
MAR 17, 03:09 PM
|
|
What a great how-to. It is nice that you take the time to share your knowledge, to many times the basic fundamentals are over looked and taken for granted. Great Job.
|
|

 |
|