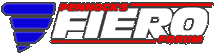

 |
Twin Disc clutch in an F23/Northstar (Page 1/13) |
|
1986 Fiero GT
|
MAY 13, 12:03 AM
|
|
|
|
1986 Fiero GT
|
MAY 13, 12:10 AM
|
|
|
|
Bozzie
|
MAY 13, 09:48 AM
|
|
Just super duper COOL !!! Nice work.
Boz
|
|
|
Raydar
|
MAY 13, 07:31 PM
|
|
Oh man! Nice work.
|
|
|
pmbrunelle
|
MAY 13, 11:40 PM
|
|
Why do you need to plug the unused bolt holes?
|
|
|
1986 Fiero GT
|
MAY 14, 10:03 AM
|
|
quote | Originally posted by pmbrunelle:
Why do you need to plug the unused bolt holes? |
|
Probably don't, really. I just wanted to. Much the same way that I hate wheels with two patterns, I didn't want my flywheel to be Swiss cheese. It's not such a fiddly job on a neutral balance flywheel with a symmetrical bolt pattern.
|
|
|
fieroguru
|
MAY 14, 01:10 PM
|
|
Did you verify the stack height to make sure everything will fit within the F23? What are you doing about the throwout bearing - typically the 7 1/4 pressure plates need a smaller diameter throwout bearing face to work best?
I am interested to hear how the drivability is, When I add a turbo, I will likely need to upgrade my current clutch setup. They guys running an organic disk say they are easy to over heat and typically get about 15000 miles before it needs to be replaced. The guys running the metallic disks have commented about them being grabby. So I am curious as to wear yours falls in the spectrum. I would suspect some of the 9" twin disk setups would have better drivability (but more mass and MOI).
I would have pressed in the plugs as well, but then simply offset the hole pattern on top of the current one (drilling part of the hole through the new plugs). This would maximize the virgin material between the bolt holes and with the plugs, the head of the bolts would be fully supported.
|
|
|
1986 Fiero GT
|
MAY 14, 01:25 PM
|
|
quote | Originally posted by fieroguru:
Did you verify the stack height to make sure everything will fit within the F23? What are you doing about the throwout bearing - typically the 7 1/4 pressure plates need a smaller diameter throwout bearing face to work best?
I am interested to hear how the drivability is, When I add a turbo, I will likely need to upgrade my current clutch setup. They guys running an organic disk say they are easy to over heat and typically get about 15000 miles before it needs to be replaced. The guys running the metallic disks have commented about them being grabby. So I am curious as to wear yours falls in the spectrum. I would suspect some of the 9" twin disk setups would have better drivability (but more mass and MOI). |
|
There's plenty of room in the F23 housing. Something like almost an inch more depth than a 282. I actually think I've got about a .250"-.375" gap between the diaphram fingers and throwout. What I'm going to do is machine an adapter to go on the face of the throwout that will take up the extra distance as well as give me the 44mm 'ring' that Tilton recommends to release the diaphram spring. I have to disassemble my F23 to reseal it anyhow, so I'll use the bellhousing half to take my measurements while I'm waiting for that.
The discs I got are the cerametallic discs. They claim 570ft./lb. holding capacity with the UH ratio pressure plate and Buff springs. I went with the UH ratio plate because it was recommended for modulation, which is what you want in a street car. We'll see how it goes, but I wouldn't even be upset about 15,000-20,000 miles out of it. That's like 2 or 3 seasons for me. Probably take me half a day to swap clutch discs at this point.
I installed a Tilton 5/8" master cylinder up front when I did the F23 install, so I shouldn't have to worry about any hydraulic issues with this setup. I'm expecting it to be up to twice as still, but I'm okay with that as the previous setup was basically a mild-mannered factory GM setup.[This message has been edited by 1986 Fiero GT (edited 05-14-2017).]
|
|
|
1986 Fiero GT
|
MAY 17, 11:00 PM
|
|
|
|
1986 Fiero GT
|
MAY 26, 08:53 PM
|
|
If anybody is still following along, I managed to drill and tap the crankshaft in my 'new' motor. Seems like it'll work just fine.
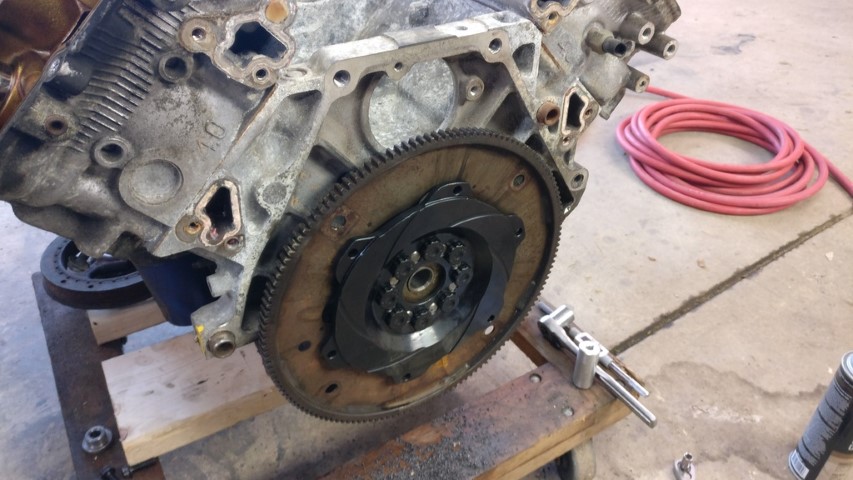
Gonna head over on Sunday to reseal the motor halves and fix the head bolts with Northstar Performance studs. I DO NOT recommend him. I had an extremely poor experience and will never be back. Having said that, I'm more than capable of machining my own 4140 inserts and using ARP studs from now on. That solution is even cheaper than his. I must give him credit for his tooling, though. It works great.[This message has been edited by 1986 Fiero GT (edited 10-02-2021).]
|
|

 |
|