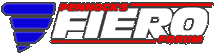

 |
How to Build a Hybrid MY8/M17 Muncie, and the Differences Between the Two (Page 1/4) |
|
NJD85GT
|
APR 04, 11:55 PM
|
|

Introduction
I didn't see hardly any info on this, so I thought I would do a writeup on this.
Many V8 swappers, myself included, want to use the econo-4 speed MY8 Muncie behind their V8 because of the really nice cruising gear, and the ratios match well with the broad torque curve of the V8. There were 7,099 of these made in ’84. However, the case is an ’84 case, and does not have the same strength as the ribbed V6 case, so many swap the gear set into the stronger case.
Many regard the V6 Muncie as the strongest of all of the Fiero manual transmissions. Due to the design of the Muncie, it is possible to keep the V6 1st and 2nd gear, and the econo 3rd, 4th, and final. I did this writeup to show how easy it is to keep the lower ratio and stronger V6 1st gear and the stronger V6 2nd gear to better handle the V8 torque. The V6 1st gear also is more useful as you can shift at a higher speed.
Reasons to build hybrid: a) The hybrid 1st gear has a 6% lower ratio over MY8, thus can shift at a higher speed (10.99 overall 1st ratio is the lowest possible ratio of all 4-speeds). b) The M17 1st gear is 5% thicker than the MY8, and thus stronger. c) The M17 2nd gear has fewer, but larger teeth than the MY8 gear, and is stronger.
Other than the gear ratios and thicknesses, there is one other difference between the MY8 and M17. The V6 Muncie uses a one piece 3rd and 4th gear, while the MY8 has a separate 3rd and 4th gear on the output shaft. As a result the spline configuration between the two shafts is different, and they are not interchangeable. In the hybrid transmission, the M17 input shaft and the MY8 output shaft and ring gear is used, the gears that are swapped are the ones that are not machined as part of the shaft or splined on.
First, the gear ratios, tooth counts, and gear thicknesses of each transmission, as well as the hybrid. Thicker gears and less, but larger teeth are generally stronger.
M17: ________________________________________________________ Gear ____ Ratio ___ Gear _____ Input __ Output _ Overall ____________________Width ____ Tooth #_ Tooth # _Ratio__ 1st _____ 3.31 ____ 0.79" ____ 16 _____ 53 _____ 12.08__ 2nd _____ 1.95 ____ 0.62” ____ 20 _____ 39 _____ 7.12___ 3rd _____ 1.24 ____ 0.62" ____ 37 _____ 46 _____ 4.53___ 4th _____ 0.81 ____ 0.58” ____ 47 _____ 38 _____ 2.96___ Final ___ 3.65 ____ 1.20” ____ 23 _____ 84 _____ _-_____
MY8: ________________________________________________________ Gear ____ Ratio ___ Gear _____ Input __ Output _ Overall ____________________Width ____ Tooth #_ Tooth # _Ratio__ 1st _____ 3.53 ____ 0.75" ____ 15 _____ 53 _____ 11.72__ 2nd _____ 1.95 ____ 0.62” ____ 22 _____ 43 _____ 6.47___ 3rd _____ 1.24 ____ 0.62" ____ 37 _____ 46 _____ 4.12___ 4th _____ 0.73 ____ 0.58” ____ 48 _____ 35 _____ 2.42___ Final ___ 3.32 ____ 1.20” ____ 25 _____ 83 _____ _-_____
Hybrid: ________________________________________________________ Gear ____ Ratio ___ Gear _____ Input __ Output _ Overall ____________________Width ____ Tooth #_ Tooth # _Ratio__ 1st _____ 3.31 ____ 0.79" ____ 16 _____ 53 _____ 10.99__ 2nd _____ 1.95 ____ 0.62” ____ 20 _____ 39 _____ 6.47___ 3rd _____ 1.24 ____ 0.62" ____ 37 _____ 46 _____ 4.12___ 4th _____ 0.73 ____ 0.58” ____ 48 _____ 35 _____ 2.42___ Final ___ 3.32 ____ 1.20” ____ 25 _____ 83 _____ _-_____
_______________________________________________ Shift Speed @ 5,500 RPM, 215-60R15 Tires (MPH): 1st – 2nd ______38_____________________________ 2nd – 3rd _____ 64_____________________________ 3rd – 4th _____ 100____________________________
_____________________________ Engine RPM in 4th Gear @ MPH: 40______1295_________________ 50______1619_________________ 60______1943_________________ 70______2267_________________ 80______2591_________________ 100_____3238_________________ 120_____3886_________________
All drawings courtesy of the 1985 Service Manual.
 Figure 0.1, Service Manual
 Figure 0.2, Cross Section
|
|
|
NJD85GT
|
APR 04, 11:56 PM
|
|
This writeup assumes all components of both transmissions are in good working order (bearings, synchronizers, etc.) and do not need replacing. These components should be replaced if they are worn. Both transmissions used in this writeup were low mileage transmissions.
Case, Disassembly
Remove shift brackets and speedo sensor (Figure 1.1 & 1.2). Leave the "z" shaped bracket on the shaft that goes into the transmission.
 Figure 1.1, Shift Brackets
 Figure 1.2, Speedo Sensor
Place the transaxle clutch side down (Figure 1.3), use shims to keep the input shaft and axle seals from touching the surface. Remove the (15) bolts securing the clutch cover to the transaxle case. Leave two bolts threaded, one on each side, to prevent the two halves from coming apart just yet.
 Figure 1.3, Case Bolts
Flip the transmission over, and remove those last two bolts. Use a plastic hammer to carefully tap the clutch cover from the transaxle case. Anaerobic sealant is used between the case and cover, instead of a gasket. (Figure 1.4, 1.5, 1.6, & 1.7)
 Figure 1.4, Clutch Side Up
 Figure 1.5, Case Halves Separated
 Figure 1.6, Gears
 Figure 1.7, Clutch Cover Removed
Remove the ring gear/differential assembly shown in Figure 1.8 & 1.9. It just lifts out.
 Figure 1.8, Removing Ring Gear/Differential
 Figure 1.9, Ring Gear/Differential Assembly[This message has been edited by NJD85GT (edited 04-14-2012).]
|
|
|
NJD85GT
|
APR 04, 11:57 PM
|
|
Removal of Internal Parts
Position the shifter shaft in the neutral position so that the shifter shaft moves freely and is not engaged in any drive gear. Bend back tab on lock and remove bolt from shifter shaft (Figures 2.1 & 2.2) Remove the shifter shaft and the shift fork shaft from the synchronizer forks as shown in Figures 2.3, 2.4 & 2.5.
 Figure 2.1, Shifter Shaft Bolt, Close Up
 Figure 2.2, Shifter Shaft Bolt
 Figure 2.3, Shift Fork Shaft Removal
 Figure 2.4, Shifter Shaft Removal
 Figure 2.5, Shifter and Shift Fork Shafts
Remove the reverse shift fork shown in Figures 2.6 & 2.7 by disengaging from the guide pin and interlock bracket.
 Figure 2.6, Reverse Shift Fork Removal
 Figure 2.7, Reverse Shift Fork Removal
Remove the lock bolt securing the reverse idler gear shaft. This bolt threads in from the outside of the case below the idler gear. Remove the gear/shaft/spacer assembly as shown in Figures 2.8 & 2.9.
 Figure 2.8, Reverse Idler Gear Removal
 Figure 2.9, Reverse Idler Gear Removal
Remove the detent shift lever and interlock assembly (Figure 2.10). Leave shift forks engaged with the synchronizers as shown in Figure 2.11. Do not remove the detent spring.
 Figure 2.10, Detent Shift Lever & Interlock Assembly Removal
 Figure 2.11, Interlock Assembly
Grasp the input and output shafts and then lift them as an assembly from the case. Note the position of the shift forks, shown in Figure 2.13, for aid when reinstalling later. Remove the shift forks (Figures 2.12, 2.13, 2.14, & 2.15)
 Figure 2.12, Shift Forks on Gear Shafts
 Figure 2.13, Shafts/Shift Forks
 Figure 2.14, Shift Forks Removed From Gear Shafts
 Figure 2.15, Input and Output Shaft Assemblies. Left: Input Shaft, From Bottom: 4th, 3rd, 2nd, Reverse, 1st. Right, Output Shaft, From Bottom: 4th, 3rd, 2nd, 1st, Pinion to Ring Gear.[This message has been edited by NJD85GT (edited 04-07-2012).]
|
|
|
NJD85GT
|
APR 04, 11:58 PM
|
|
Input Shaft Disassembly, MY8 and M17
Slide the left hand bearing and 4th gear from input shaft. They slide off very easily. (Figure 3.1)
 Figure 3.1, Bearing and 4th Gear Removed
Remove brass blocker ring, Shown in Figure 3.2. Remove the snap ring from the 3-4 synchronizer (Figure 3.3).
 Figure 3.2, Brass Blocker Ring Removed
 Figure 3.3, Snap Ring (On Shaft Next To Synchronizer Behind Splines)
Slide 3rd gear and 3-4 synchronizer from input shaft. They also should slide off easily, a press should not be needed as shown in the figure from the manual (Figures 3.4, 3.5, & 3.6).
 Figure 3.4, From Right: Bearing, 4th Gear, Brass Blocker Ring, Synchronizer Sleeve With Snap Ring in the Middle (Do Not Need to Remove From Synch. Hub), Synchronizer Hub With 3rd Gear Underneath
 Figure 3.5, Bare Input Shaft
 Figure 3.6, Removing 3-4 Synch. and 3rd Gear (Input)[This message has been edited by NJD85GT (edited 04-07-2012).]
|
|
|
NJD85GT
|
APR 04, 11:59 PM
|
|
Input shaft Reassembly, Hybrid
Lubricate all parts prior to reassembly.
Locate the M17 input shaft, and place the MY8 3rd gear onto the shaft, oriented toward the 3-4 synchronizer. Install the brass blocker ring onto the gear cone, then install the 3-4 synchronizer, using an appropriate cylinder to contact the hub, near the shaft. Do not press on the sleeve portion (Figure 4.1). Both synchronizer hubs are a press fit to the shafts. I just hand placed them on the shaft, no cylinder needed.
 Figure 4.1, Installing 3rd Gear and 3-4 Synchronizer.
Install the snap ring to retain the 3-4 synchronizer. Be sure to position snap ring with beveled edges away from synchronizer for later access with snap ring pliers (Figure 4.2).
 Figure 4.2, Installing Snap Ring.
Install brass blocker ring. Slide the MY8 4th speed gear onto shaft, oriented toward the 3-4 synchronizer and slide left hand bearing onto the shaft.[This message has been edited by NJD85GT (edited 04-13-2012).]
|
|
|
NJD85GT
|
APR 05, 12:00 AM
|
|
Output Shaft Disassembly, MY8
Using support plates behind 4th gear, press on the end of the output shaft to remove 4th gear and the left hand bearing (Figures 5.1 - 5.3). I used a small 5-ton press.
 Figure 5.1, MY8 Assembled Output Shaft. Notice the separate 3rd & 4th Gears.
 Figure 5.2, 4th Gear and Bearing Removed.
 Figure 5.3, Pressing 4th Gear Off.
Remove the snap ring retaining 3rd gear. Slide the 1-2 synchronizer assembly into first gear position to allow press plates to support 2nd gear. Press 2nd speed gear and 3rd gear from the output shaft. Remove the brass blocker ring (Figures 5.4 & 5.5).
 Figure 5.4, Pressing 2nd & 3rd Gears Off.
 Figure 5.5, Pressing 2nd & 3rd Gears Off.
Remove the snap ring retaining the 1-2 synchronizer. Using press plates behind 1st speed gear, press 1st gear and 1-2 synchronizer from the output shaft (Figures 5.6 & 5.7). I was able to do this without the press.
 Figure 5.6, Pressing 1st Gear Off.
 Figure 5.7, Disassembled MY8 Output Shaft.[This message has been edited by NJD85GT (edited 04-13-2012).]
|
|
|
NJD85GT
|
APR 05, 12:01 AM
|
|
Output Shaft Disassembly, M17
Remove the retainer from the left hand end of the shaft. The retainer and shaft are designed with LEFT HAND threads. This retainer uses a triple square bit, and is torqued to 45 ft•lb, and I was unable to remove it without starting to strip it. Because you do not need to use the M17 output shaft for this hybrid transmission, I used a grinder and cut the flange off the retainer. Using support plates behind 4th gear, press on the end of the output shaft to remove 3rd/4th gear and the left hand bearing (Figures 6.1 - 6.4). Third and fourth gear is a one piece gear on the M17 transaxle.
 Figure 6.1, Assembled M17 Output Shaft
 Figure 6.2, 3rd/4th Gear Removed.
 Figure 6.3, 3rd/4th Gear.
 Figure 6.4, Pressing Off 3rd/4th Gear.
Slide 2nd speed gear from the output shaft. Remove the brass blocker ring. Remove the snap ring retaining the 1-2 synchronizer. (Figure 6.5).
 Figure 6.5, 2nd Gear Removed.
Using press plates behind 1st speed gear, press 1st gear and 1-2 synchronizer from the output shaft (Figure X). I was able to do this without the press.
 Figure 6.6, Pressing Off 1st Gear.
 Figure 6.7, M17 Output Shaft & Gears.
 Figure 6.8, M17 Output Shaft.[This message has been edited by NJD85GT (edited 04-14-2012).]
|
|
|
NJD85GT
|
APR 05, 12:02 AM
|
|
Output shaft Reassembly, Hybrid
Lubricate all parts prior to reassembly.
Locate the MY8 output shaft, and place the M17 1st speed gear onto the shaft, oriented toward the 1-2 synchronizer. Place the brass blocker ring onto the gear cone, then install the 1-2 synchronizer using an appropriate cylinder to press on the hub, near the shaft. Do not press on the sleeve portion (Figure 7.1). I just hand placed them on the shaft, no cylinder needed.
 Figure 7.1, Installing 1st Speed Gear and 1-2 Synch.
Install the snap ring to retain the 1-2 synchronizer. Place the brass blocker ring into position. Place the M17 2nd speed gear onto the shaft, oriented toward the 1-2 synchronizer, then press the MY8 3rd gear onto the shaft, with its hub toward 4th gear. Use an appropriate cylinder to contact 3rd gear hub near the shaft (Figure 7.2). I inverted the shaft, placed 3rd gear on support plates, and pressed on the right hand end of the shaft with my press. When you can install the snap ring in the groove, you have pressed enough. (Figure 7.3).
 Figure 7.2, Installing 2nd and 3rd Speed Gears.
 Figure 7.3, Pressing 3rd Gear Into Place.
Install snap ring to retain 3rd gear. Press the MY8 4th gear onto the shaft, with its hub toward 3rd gear, using support plates. Install left hand bearing cone on the shaft. (Figure 7.4).
 Figure 7.4, Installing 4th Gear and L.H. Bearing.[This message has been edited by NJD85GT (edited 04-13-2012).]
|
|
|
NJD85GT
|
APR 05, 12:03 AM
|
|
The following section is optional, but highly recommended to set the correct pre-load on the bearings. This requires special shim selector tools, I bought mine off of Ebay for $17.
Shim Selection
Place the input and output shaft assemblies and the MY8 differential assembly into their installed positions.
Remove the input, output, and differential bearing cups and shims from the clutch cover.
Place the (3) right hand bearing races onto their respective bearings.
Position (3) gages; J-26935-2 on input bearing and J-26935-4 onto output bearing. Be sure the bearing races fit smoothly into the bores of the gauge tools (Figures 8.1 - 8.5).
 Figure 8.1, Shim Selector Kit.
 Figure 8.2, Shim Selector Kit Instructions.
 Figure 8.3, Shim Selector Kit.
 Figure 8.4, Gauges In Position.
 Figure 8.5, Gauges In Position.
On J-26935-4, (output shaft), install oil shield retainer into bore on top of tool.
Carefully assemble the clutch cover over the (3) gages and onto the case, using (7) spacers placed evenly around the perimeter. Retain with bolts provided (Figure 8.6).
 Figure 8.6, Compressing Gauges.
Draw the cover to the case by tightening alternately and gradually. Torque bolts to 10 ft•lb. This will compress all three gauge sleeves. Rotate each gage to seat the bearings. Rotate the differential case through three revolutions in each direction.
With the three gauges compresses, the gap between the outer sleeve and the base pad is larger than the correct preload shim at each location. Carefully compare the gap to the available shims. Determine the largest shim that can be placed into the gap and drawn through without binding. Then use the next shim size smaller on the output shaft and differential for reassembly. On the input shaft, use a shim 2 sizes smaller. If end play occurs, use the next larger shim sizes (Figure 8.7).
 Figure 8.7, Measuring Gap.
When each of the three shim sized has been selected, remove the clutch cover, (7) spacers and (3) gauges. Place the selected shims into their respective bore in the clutch cover, add the metal shield and then install the bearing cups.[This message has been edited by NJD85GT (edited 04-13-2012).]
|
|
|
NJD85GT
|
APR 05, 12:04 AM
|
|
|

 |
|