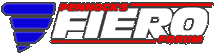

 |
Blooze Own: An F355 Six Speed N* Build Thread (Page 92/126) |
|
Bloozberry
|
JAN 28, 07:14 PM
|
|
Thanks Bob. Stealing a page from Yarmouth Fiero's Book of Convertible Design, I'm removing the lower half of the two Z sections that form the base of the rear window support, and replacing it with a much stiffer beam. In the drawings I posted earlier, this new cross car beam will serve as a solid mount for the stationary end of the coil-overs, the two engine torque struts, the deck lid hinges, and the new MR2 rear glass.
I wasn't looking forward to removing the lower half of the OEM channel because Yarmouth Fiero said it was a real pain in the butt. So I got myself mentally prepared for hours of sitting in the engine bay and drilling out spot welds, but in the end I found it went really quickly, probably because I had already removed the hinge boxes:

Once the spot welds were turned into a little pile of metal shavings on my floor, I tried to remove the Z section by pulling down on it but was prevented by a pair of little supporting flanges that are part of the upper frame rail. I made quick work of those by lopping them off with the die grinder (the red oxide primer is from the previous owner when he stretched the frame):

The Z section needed a little coaxing to remove because I couldn't get to two of the spot welds very well that were tucked up next to the frame rail, but it wasn't going to win the battle. I was actually surprised to see surface rust inside the channel... nothing serious, but it does make me wonder how it got there. It doesn't look like the inside surface of the channel was primed or painted at the factory.

After a few tugs it bent at the big hole I made when I removed the left hinge box, and then it just fell out:

Sitting on the shop floor with the remnants of the spot welds... (my pile of removed OEM sheet metal is getting bigger... I should take a picture of it when I'm done.)

Finally, here's what the firewall looks like without the lower half of the OEM cross-car beam. I'll need to sand off the rust and re-prime the area before the next step, which is cutting and fitting the new beam:

(Edit: forgot to add the last photo!)[This message has been edited by Bloozberry (edited 01-28-2014).]
|
|
|
Sage
|
JAN 28, 07:45 PM
|
|

Can hardly wait to see the next step, and eagerly looking forward to the MR2 glass install.
Keep it coming....we're still watching.
HAGO!
|
|
|
Yarmouth Fiero
|
JAN 28, 08:44 PM
|
|
Great job removing the metal Blooz. You did a much neater job of it than I did. I found the hinge boxes to be the biggest pain to remove because the welds were so random. I'm sure the spot welding robot went nuts the day they built my car.
Looking forward to seeing your transverse frame in place. I'm hoping it will similar to mine in cross section so we can develop rear deck hinges that fit both cars.
Not that we are counting..... but my scrap Fiero metal pile weights about 70 lbs so far.
|
|
|
Bloozberry
|
JAN 28, 09:25 PM
|
|
quote | Originally posted by Yarmouth Fiero: I'm hoping it will similar to mine in cross section so we can develop rear deck hinges that fit both cars. |
|
Not to worry... I don't plan to reinvent the wheel. It will exactly as yours is.
|
|
|
Bloozberry
|
FEB 03, 04:58 PM
|
|
To make the new firewall cross member, I re-read Yarmouth Fiero's thread to be sure our cars would be the same in this area since we'll be sharing the same body molds for our cars despite his being a convertible and mine being a berlinetta. I used his idea to take a 3" x 4" x 1/8 wall rectangular tube as the basis for the cross member. The firewall is sloped at about 18 degrees from vertical though, so the tubing has to be modified to fit the firewall snuggly yet have the rear edge vertical. To sort through how I would do this as well as where I would need some flanges on the cross member to weld it to the chassis, I made a cardboard template:

And since Yarmouth Fiero didn't explain why he had drilled several large holes in his firewall, the template helped me figure it out. It seems there are five "bumps" along the top of the sheet metal that protrude into the engine bay and would prevent the cross member from sitting flush against the firewall. This view is from inside the cabin so you'll have to use your imagination what the bumps look like from inside the engine bay:

I found that a 2" hole saw made a nice clean incision, and left a great way to rosette weld the hidden front side of the new cross member to the firewall:

With that out of the way, I bought the materials I'd need: 60" of the rectangular tubing (not a particularly popular size at your local metal supplies shop!) and the same length of some 3" x 1/8" flat bar.

To make the right angled trapezoidal shape of the cross member, I lopped off all of one of the 3" walls of the tubing, and a portion of the adjacent 4" wall. And, in a rare picture of me (not unlike Wilson in Home Improvement), here I am behind my fence making sparks fly with a cut off wheel in an angle grinder:

I think I went through an entire cut-off wheel to zip through a total of 10 linear feet of steel. My wife, who is building some cabinets in the other half of the shop, wasn't too happy with the smell of burning steel. Women. Here's the sectioned tube:

Seems like an awful waste to cut all this material off only to replace it, but then there would be absolutely no way just to cut say, an inch out of one wall and bend it along the entire length of the tube to close it up at the correct angle. I'm sure I'll find a use for the lopped off steel at some point in the project.
|
|
|
fierogt28
|
FEB 03, 09:30 PM
|
|
Ahhh, Blooze...I love the humor in your threads. 
I guess if there would be a fence and seeing you making sparks fly, I'd say "you got something cook'in Wilson"??
"No, no...just working on this old fiero..." lol
"What year Wilson??", etc...
Nice update for the new year, and hope to see many more ideas / craftsmanship. 
Thanks,------------------ fierogt28
88 GT, Loaded, 5-speed. 88 GT, 5-speed. Beechwood interior, All original.
|
|
|
Will
|
FEB 04, 10:01 AM
|
|
quote | Originally posted by Bloozberry: Seems like an awful waste to cut all this material off only to replace it, but then there would be absolutely no way just to cut say, an inch out of one wall and bend it along the entire length of the tube to close it up at the correct angle. |
|
Slot the face of the tube on a mill  That should be precise enough that it would bend closed at the correct angle.
|
|
|
Yarmouth Fiero
|
FEB 04, 12:53 PM
|
|
quote | Originally posted by Bloozberry:
And since Yarmouth Fiero didn't explain why he had drilled several large holes in his firewall, the template helped me figure it out. . |
|
Oops..... sorry about that Blooz. 
Edit to add: On page 6 of my thread you'll notice my transverse beam suddenly developed a mysterious seam in the middle. As hard as I tried to prevent it, my beam bowed when I welded the 3" x 1/8" flat bar back on. Just an FYI so you don't think I've been keeping any more secrets.  [This message has been edited by Yarmouth Fiero (edited 02-04-2014).]
|
|
|
355Fiero
|
FEB 04, 07:13 PM
|
|
Continued outstanding work Blooz. Incredible fab skills.
Keep up the great work and I am looking for to seeing the rear suspension under tension with everything sitting on the floor at ride height.
Cheers Don
|
|
|
Bloozberry
|
FEB 04, 10:17 PM
|
|
Thanks Fierogt28, Will, Yarmouth Fiero, and 355Fiero for all your comments. I too am looking forward to seeing the chassis sitting on all four wheels. It won't be too much longer now.
Continuing on with the firewall cross member, the next step was to bend some flanges at either end. I find bending flanges is always a bit of a trial and error process since knowing where to start the bend depends on how accurate your bending machine is. In my case, I don't have a bending machine so getting a precise distance between the flanges at opposite ends of the cross member also took some luck. The dies I have for my hydraulic press couldn't be used because there are just too many flanges to get in the way. So I did it the "shade-tree" mechanic's way. I marked a line where I wanted the flange to be, then moved it another 1/8" further to account for the thickness of the material, and then guessed I'd need about another 1/16" for the bend radius. I then drilled 1/4" holes in the corners of the tube to act as clean stops for the angle grinder and then sliced the tube lengthwise up to the holes:

Then I sandwiched the side of the tube between a couple 1/2" steel plates I had lying around and used a high tech 5 lb mallet to bend the flanges :

Once all three flanges were bent at one end, I double checked how close my flanges were to where I had actually wanted them, then made a few adjustments to locating my bend lines at the other end before doing them. I came within about a millimeter from the overall distance I needed between the two ends of the tube but easily tweaked it a bit until it fit tightly. I wanted to prime the inside of the tube so that was easiest while the fourth side was not yet welded on.

I then tacked the 3" x 1/8" steel bar to the tube in many places to keep it from deforming while final welding it, then hit it up with a full zap:

By this time I had already trial-fitted the new firewall cross member a dozen times so I was getting good at knowing just how to wiggle and jiggle it into place, and just where to hit it with the rubber mallet to seat it. Here's the final mock up before tack welding it:

And a close up of how the flanges tie into the upper frame rail:

Next up is cutting and fitting two vertical supports for the new cross member. They'll rise up from the lower frame rail to the underside of the cross member.
|
|

 |
|