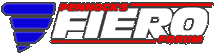

 |
Tripods comparison for Hybrid F40 Axle construction (Page 1/1) |
|
Daviero
|
MAR 28, 05:28 PM
|
|
Back in 2009, FieroGuru posted details of his hybrid tripods for F40 axles. The topic is archived here about 2/3 down page 1. The basics of the hybrid tripod is:
quote | Axles
The tripods spline for the F40 is 27 and there are several sources of tripods that will fit the F40 transmission: G6/F40 stock axles Cobalt/Redline Supercharged 5 speed axles 1999 Saab 9-5 GM 5 speed autos (Torrent, Equinox, Aura, etc...)
For my first set of axles, I will be using hybrid tripods and factory GM axles. Essentially taking 2 tripods, and using the F40 compatible spline part with fiero and corsica style tripod cages and welding them together.
The passenger side will be using a 96 Corsica axle (Passenger side, 4speed auto). It has fiero compatible outer CV, the shortest GM axle shaft, and the same axle shaft splines as the maual fiero. The corsica rollers are different than the fiero, so I will use the Corsica roller cage. For the splined part for the transmission, I will use an OEM torrent tripod. |
|
I am replacing my Northstar 5 sp with an LS4 6 spd and will build custom tripods modeled after FieroGuru's to solve the axle issue.
QUESTION:
The Corsica tripod is only slightly smaller than the 88 Fiero manual tripods which are also common to Grand Am, Grand Prix, Lumina and maybe others too. The axle shafts are the same dia and spline. The star bearing insert is about the same size overall but have some visible differences in the bearings themselves. The radius of the contact point between the star and the tulip are about the same so one might expect the same torque capacity? Which one might be stronger or would there be any difference? It might be splitting hairs but the Lumina/Grand Prix tripods seem to be more plentiful and although I have 2 of the Corsica tripods and a short drivers side axle shaft, I'm looking for a reason to not use the Corsica tulips because they might be hard to replace if I break one. So I could use the Corsica short shaft with a Lumina derived hybrid tulip instead. Your opinions are welcome! [img] [/img]
------------------ Daviero - 88 N* 5spdGT[This message has been edited by Daviero (edited 03-29-2024).]
|
|
|
fieroguru
|
MAR 28, 08:01 PM
|
|
I fabricated the Corsica hybrid axle in March of 2010... wow hard to believe it has been 14 years... and it has lasted 55K miles.
At the time, I just kept everything Corsica to keep it simple. If I fragged an axle while on the HRPT (and 500+ miles from home), I wanted to be able to swap a replacement in with the least amount of work. I also picked up a spare axle just in case, and took it with me on the first couple of HRPTs, but eventually it just started (and still is) gathering dust on the shelf.
It wasn't a factor in the original decision, but looking at the pictures, the Corsica outer tripot housing had more squared cups and creates nice overlap zones for the welding process.
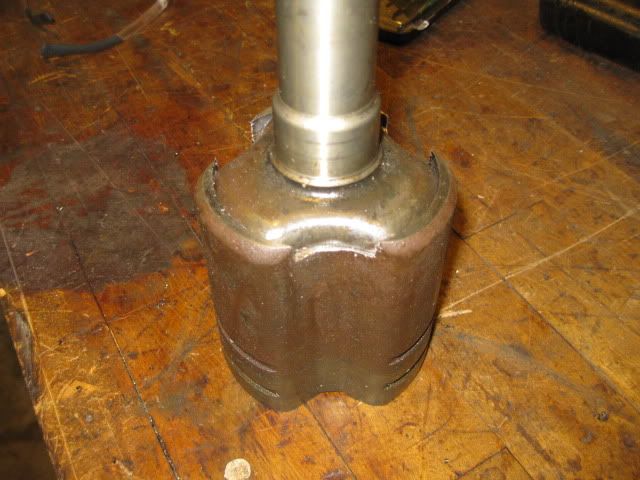 [This message has been edited by fieroguru (edited 03-28-2024).]
|
|
|
Daviero
|
MAR 29, 09:58 AM
|
|
I was hoping you'd chime in Fieroguru. Thanks. I'm perhaps late to the game on this and your details and experiences are invaluable! Yes the squared out Corsica Tulip also matches the shape of the Torrent tulip better than the GrandAm/Lumina one. Its a shame the Torrent axle isn't 27 mm like the Fiero, Corsica, Lumina ones. When or if the need to replace a Corsica star insert comes, it might be hard to find one now though, thus my incentive to use another more plentiful version. Your achieving 55k on them is a good testament though. The deciding factor might be in the Corsica tulip being double grooved for the boot, and your need to cut down the driver side to get full axle articulation. The Lumina ones are only single groove and might not provide the required articulation. Perhaps a Lumina hybrid tulip can be shortened on the other end before attaching the Torrent stub. I'll study this some more and decide. I do intend on using the same hybrid tulip on both sides though, just for symmetry if nothing else. I see you kept the Saab tripod on the passenger side. ------------------ Daviero - 88 N* 5spdGT
|
|
|
fieroguru
|
MAR 29, 01:53 PM
|
|
On the passenger side, you are trying to gain 1" so you can keep the stock Fiero axle. The one I had a buddy make up used a Saab splined end because it had a longer transition to the cage and a Fiero tripot housing.
The big thing to know is the F40 moves the axle centerline closer to the engine. So while the mockup with a SBC/F40 was fine with the Fiero sized tripot housing, when I switched to the LS4, there was zero chance of the Fiero sized tripot housing clearing the oil pan/block flange. Even the smaller diameter G6 F40 tripot barely clears with some clearancing to the flange still needed.
So mock up the transmission to the N* block and check how much room is there for a Tripot before you start down the modified tripot path.
|
|
|
Daviero
|
MAR 29, 04:28 PM
|
|
Yes, mock up for sure. The Northstar is out and gone though, I’m on the LS4 route but have been stuck on the accessory drive layout for a very long time - I put a C4 power rack (2 turns lock to lock🙂) in the car years ago so I needed to figure a way to route the belt for p/s, a/c, alt and the water pump. I’m glad to be on axles now. I’ll post what it did when I’m further along.
|
|
|
Daviero
|
APR 20, 11:21 AM
|
|
FieroGuru, what was your weld procedure for your hybrid tripot? I cannot find any definitive info on stock tripot alloys, other than it might be case hardened 1050, and that aftermarket higher end units are 4130 or 4340. Either way, a high carbon equvalant, also confirmed them ringing like a tuning fork when struck and by less than ideal machinability. Given this, just welding it like a lower carbon steel would result in weld cracks upon cooling? Is a pre-weld heat to 500F and a post weld cool down from about 400 to ambient over 2 hours appropriate? You must have gotten yours right as proven by the use you’ve had from it!
|
|
|
fieroguru
|
APR 20, 01:25 PM
|
|
The fiero tripot cup was pretty hard on the spline end - not so much at the open end. If I was to do it again, I would use a cutoff wheel to cut both cups off while leaving the spline end with about 1/4" or less of the cup. Then machine the interconnecting lips to center the spline end on the cup.
The only "trick" I used for welding was to clamp the assembled tripot in the mill using a center punch and raising the mill bed. Tacked in the 6 overlapping corners to hold everything in place, then cranked the welder to 5 (175A) and welded the outside. I welded about 6 lengths for the outside. Once it cooled, I welded the inside in a single pass.
No special pre or post heat treatment, but it wouldn't hurt to heat the assembly once tacked to about 3-400 degrees prior to welding... Especially if you are going to use a smaller welder. If you do preheat them, you don't need your welder set as high. Last thing you want is to burn through.
I also applied a couple of layers of painters tape to the roller surfaces to keep the welding splatter off them - it will catch on fire while welding, but just keep on welding until you are done.[This message has been edited by fieroguru (edited 04-20-2024).]
|
|
|
Daviero
|
APR 21, 07:41 PM
|
|
Perfect and thanks. Your advice is in line with what I had planned, except to tack I was planning on using my hydraulic press and preheat for them too.
|
|

 |
|