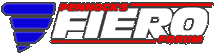

 |
EXHAUST MANIFOLD REPLACED (Page 1/1) |
|
eti engineer
|
JAN 23, 09:11 AM
|
|
Just replaced the front exhaust manifold and the rebuilt engine sounds great!! It can be done while the engine is in the car, but plan on a whole day and using the word "F__K!!!" like a comma while getting the work done!!! Thanks to you guys for the help and for selling me the manifolds without taking all my retirement savings to buy them. I actually now have another extra front manifold and one rear one. My question is, looking at the attached photo, would it be worth getting this one welded, or is it too far gone? What type of metal are these manifolds? Thanks in advance for your answers...
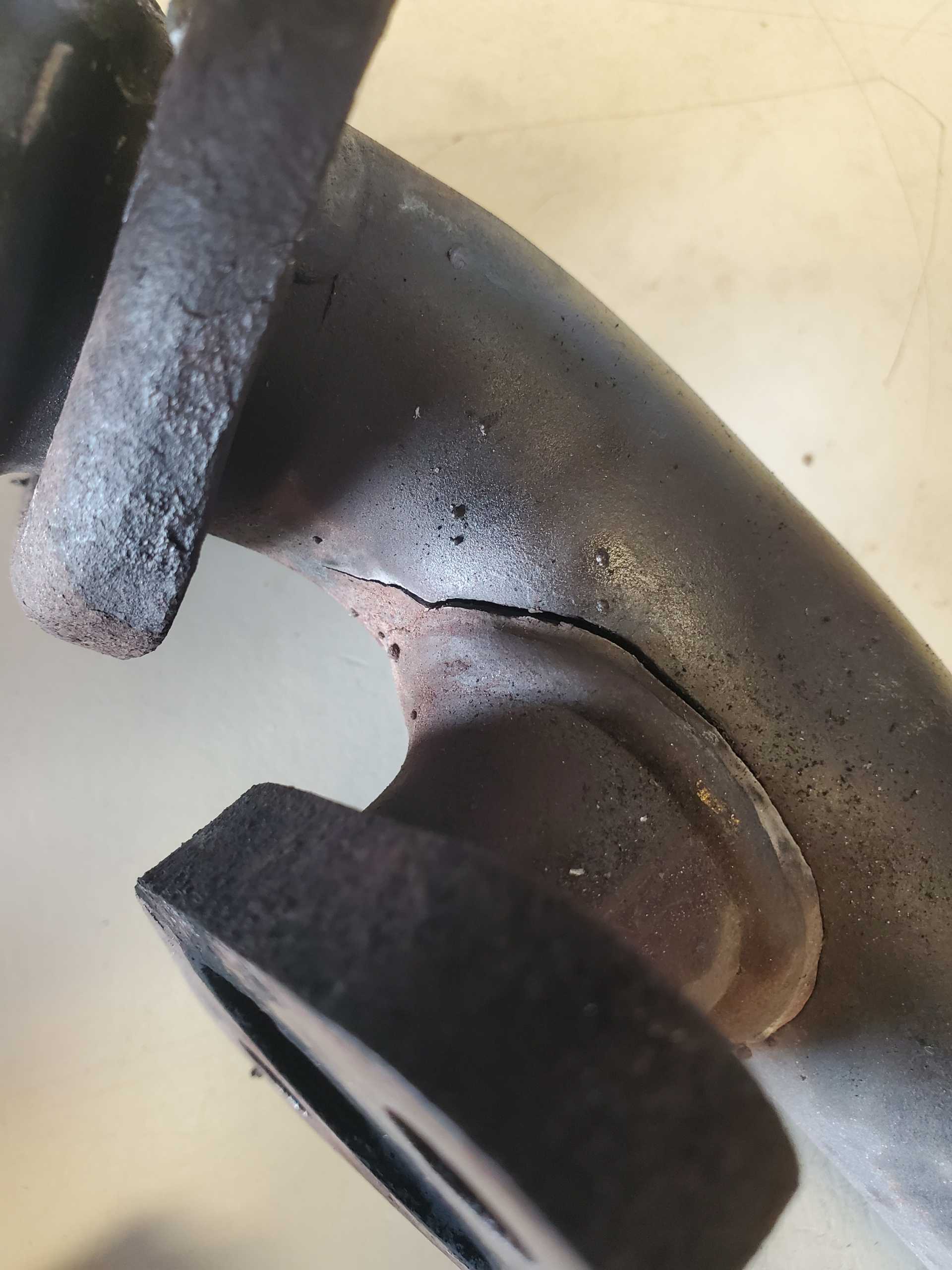 [This message has been edited by eti engineer (edited 01-23-2022).]
|
|
|
Raydar
|
JAN 23, 09:18 AM
|
|
That's a common place for them to crack. (Probably right at #6... right?) I'm sure that others will jump in with suggestions, but when you get it welded, bolt it to an old head (preferably) or a stiff piece of metal stock. Otherwise it will warp, due to the uneven heating and cooling during the welding process. You can also look inside the ports and see where the restrictions are. You can grind away a great deal of those restrictions, but be careful. You can compromise the welds where the pipes are joined. (Others just have the welds reinforced, and then grind away all of the restriction.)
Edit - Make sure that your exhaust system is not placing a lot of strain on your manifolds. You should at least have a hanger or springs on the left corner, where the pipe turns towards the cat. Also be careful of rain water spilling onto a hot exhaust. GM removed the weather seal at the front edge of the decklid (most of them, anyway) during one of the recalls.  [This message has been edited by Raydar (edited 01-23-2022).]
|
|
|
A_Lonely_Potato
|
JAN 23, 10:42 AM
|
|
quote | Originally posted by Raydar:
I'm sure that others will jump in with suggestions, but when you get it welded, bolt it to an old head (preferably) or a stiff piece of metal stock. Otherwise it will warp, due to the uneven heating and cooling during the welding process.
|
|
100% do that. When I did my trunk side header(not a stock one, but point still stands) I did not have it mounted to anything. It slid right off, but after welding it, putting it back on was a nightmare. It was just barely warped, but enough that it wouldn't slide on.
|
|
|
cvxjet
|
JAN 23, 11:25 AM
|
|
I must have fergots to send you this pic of the most necessary "tools" needed for working on Fieros....Sorry;
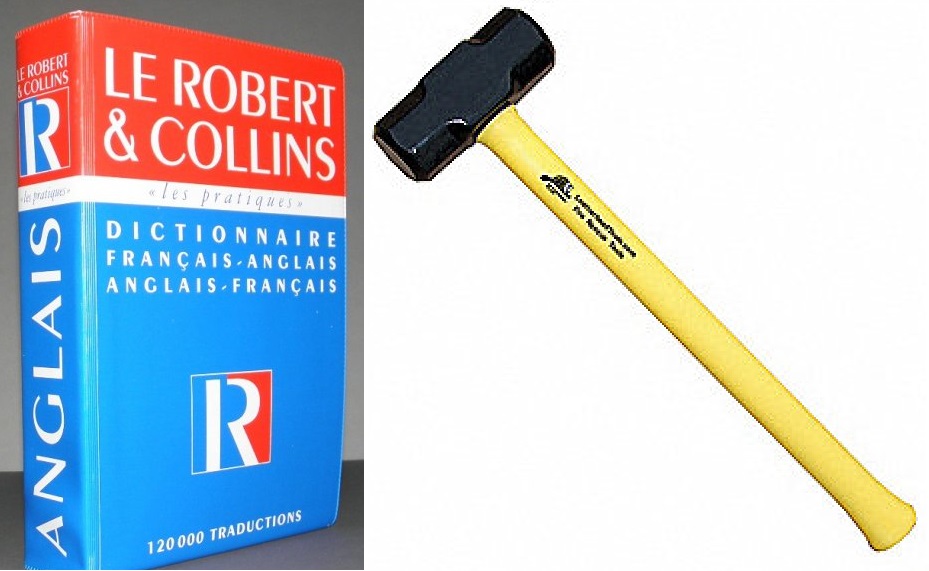 [This message has been edited by cvxjet (edited 01-23-2022).]
|
|
|
pmbrunelle
|
JAN 23, 08:11 PM
|
|
The manifold tubes are a cheap stainless; they appear to be 400-series. The flanges are mild steel. The crack can be ground out and rewelded. If you don't have a spare head, you can use a Rodney Dickman manifold welding jig.
Normally, I do suggest bellows, but you wouldn't be able to do that sort of modification and remain smog-legal in California.
|
|
|
reinhart
|
JAN 25, 09:18 AM
|
|
I've read a lot of people suggesting that the manifolds will warp if not bolted down while being welded due to the heat.
My question is, if they warp so easily due to heat, why does it matter if they warp when being welded as once they are bolted onto the engine and run through a few heat cycles, they will warp to where they fit best?
I did see one commenter say that he couldn't get the manifold on after it warped but the later design has slotled bolt holes so that shouldn't be a problem.
|
|
|
A_Lonely_Potato
|
JAN 25, 10:55 AM
|
|
quote | Originally posted by reinhart:
I've read a lot of people suggesting that the manifolds will warp if not bolted down while being welded due to the heat.
My question is, if they warp so easily due to heat, why does it matter if they warp when being welded as once they are bolted onto the engine and run through a few heat cycles, they will warp to where they fit best?
I did see one commenter say that he couldn't get the manifold on after it warped but the later design has slotted bolt holes so that shouldn't be a problem. |
|
Even with slotted bolt holes, if the manifold warps in certain ways they won't help. If the manifold bends in the way as shown below, it still won't go on without a lot of fighting. I'm not sure if running some lag bolts into a 4x4 would be strong enough to hold it in the proper position, maybe someone else knows if that would work?
|
|
|
reinhart
|
JAN 25, 01:49 PM
|
|
Well that would be a massive amount of warping if they wouldn't even fit over the studs or bolts.
I remember reading several posters that talked about going so far as, after welding, putting the manifold on a belt sander to make sure every leg is perfectly flat relative to the others. But again, if they are that flexible just from getting hot, then a few hours of running will easily get them flat against the engine. As long as the manifold can fit over the studs/bolts, it can be bolted in place and then double checked for tightness after say 100 miles of driving when the bolts can be tightened to spec.
|
|
|
A_Lonely_Potato
|
JAN 25, 07:39 PM
|
|
quote | Originally posted by reinhart:
Well that would be a massive amount of warping if they wouldn't even fit over the studs or bolts.
|
|
Mine warped enough that it did not fit. I kinda forced it back on, so it's bound to be a struggle to get it off again whenever that is  [This message has been edited by A_Lonely_Potato (edited 01-25-2022).]
|
|

 |
|