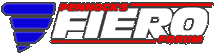

 |
The White Bug (Page 42/42) |
|
pmbrunelle
|
MAR 04, 08:26 PM
|
|
quote | Originally posted by Will: I guess if you only need to make two, that's a fine way to do it... a part-off tool would be MUCH easier. |
|
Besides having to buy (or grind) a tool to do that, I didn't want to deal with the disc coming loose at the end of the cut and possibly smashing/jamming into something.
I also thought about roughly cutting off the disc with an angle grinder + abrasive cutoff wheels, but that would have required many cutoff wheels, and I would have been left with a polygon shape needing to be turned on the lathe. I don't really like cutting polygons into round shapes; I'm not a fan of interrupted cuts like that.
For three hubs (I wanted a spare!), the method was workable, but tedious.
Ideally, I think it would be best to use an endmill to mill a groove to separate the disc from the hub; either conventional mill with rotary table, or CNC. I didn't have either of these tools at my disposal.
quote | Originally posted by Will: The front LeBaron rotor has a smaller rotor pilot than the rear rotor. It's also slightly smaller outside diameter, but it fits the Fiero rotor pilot without modification, IIRC. |
|
That's a good suggestion / good info.
I looked at pics on Rockauto, and it seems like that rotor has a rather shallow rotor hat. My caliper-to-wheel clearance is quite tight as things are now; I think that might turn into interference with the front LeBaron rotor! I'll stay on my current path for now.
|
|
|
zkhennings
|
MAR 08, 02:32 PM
|
|
The Grizzly Rotary table has been a great addition to the Bridgeport at work, not too expensive either, and nice for making cuts that are not 90* to one another in addition to doing circular things. Can be mounted vertically or horizontally.
The other way you could have rough cut the rotor off is with a jig saw and a steel cutting blade, it does a decent job, I have done some circular cuts in 0.25" steel with it. Not the speediest operation but much better than using cutoff wheels.
Nice work though, hope you get to enjoy the car this summer now that you have your hubs sorted, I am very curious to hear about how you like the car with your anti dive mod, I would like to do something similar.
|
|
|
Will
|
MAR 08, 06:12 PM
|
|
quote | Originally posted by pmbrunelle:
Besides having to buy (or grind) a tool to do that, I didn't want to deal with the disc coming loose at the end of the cut and possibly smashing/jamming into something.
I also thought about roughly cutting off the disc with an angle grinder + abrasive cutoff wheels, but that would have required many cutoff wheels, and I would have been left with a polygon shape needing to be turned on the lathe. I don't really like cutting polygons into round shapes; I'm not a fan of interrupted cuts like that.
|
|
Sounds like you're talking about making the cut axially through the rotor. I'm talking about making the cut radially through the hat section.
|
|
|
pmbrunelle
|
MAR 08, 10:26 PM
|
|
quote | Originally posted by zkhennings: Nice work though, hope you get to enjoy the car this summer now that you have your hubs sorted, I am very curious to hear about how you like the car with your anti dive mod, I would like to do something similar. |
|
The snow is melting fast, so I'm quite looking forward to the summer and getting the car ready!
quote | Originally posted by Will: Sounds like you're talking about making the cut axially through the rotor.
|
|
Yes, that's what I meant.
quote | Originally posted by Will: I'm talking about making the cut radially through the hat section. |
|
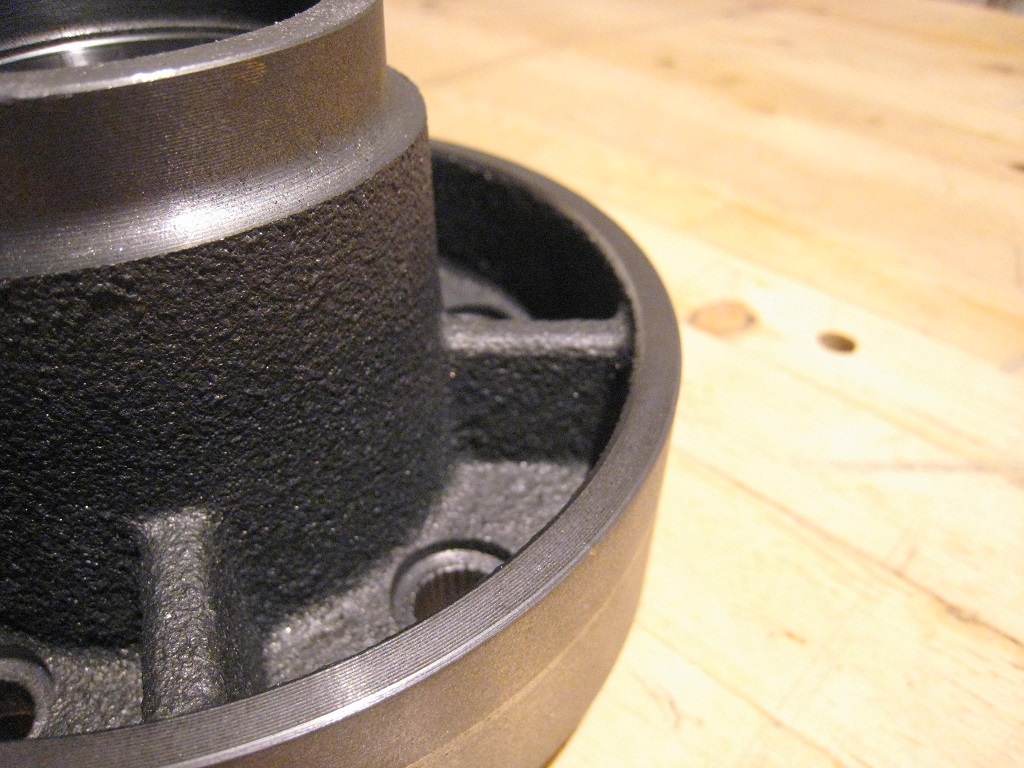
I see what you mean; in your proposition, the ribs keep the disc attached to the hub. Then, as a second step, the ribs could be cut with a small cutoff wheel to free the disc.
I wanted to keep the hat+rib area intact, as I wasn't sure how much material could be removed from there while keeping the hub strong enough. In comparison though, the rear hubs are a lot more flimsy-looking, yet they seem adequately strong.[This message has been edited by pmbrunelle (edited 03-08-2024).]
|
|
|
pmbrunelle
|
MAR 15, 05:19 PM
|
|
Reaming the lug stud holes to 12.5 mm:
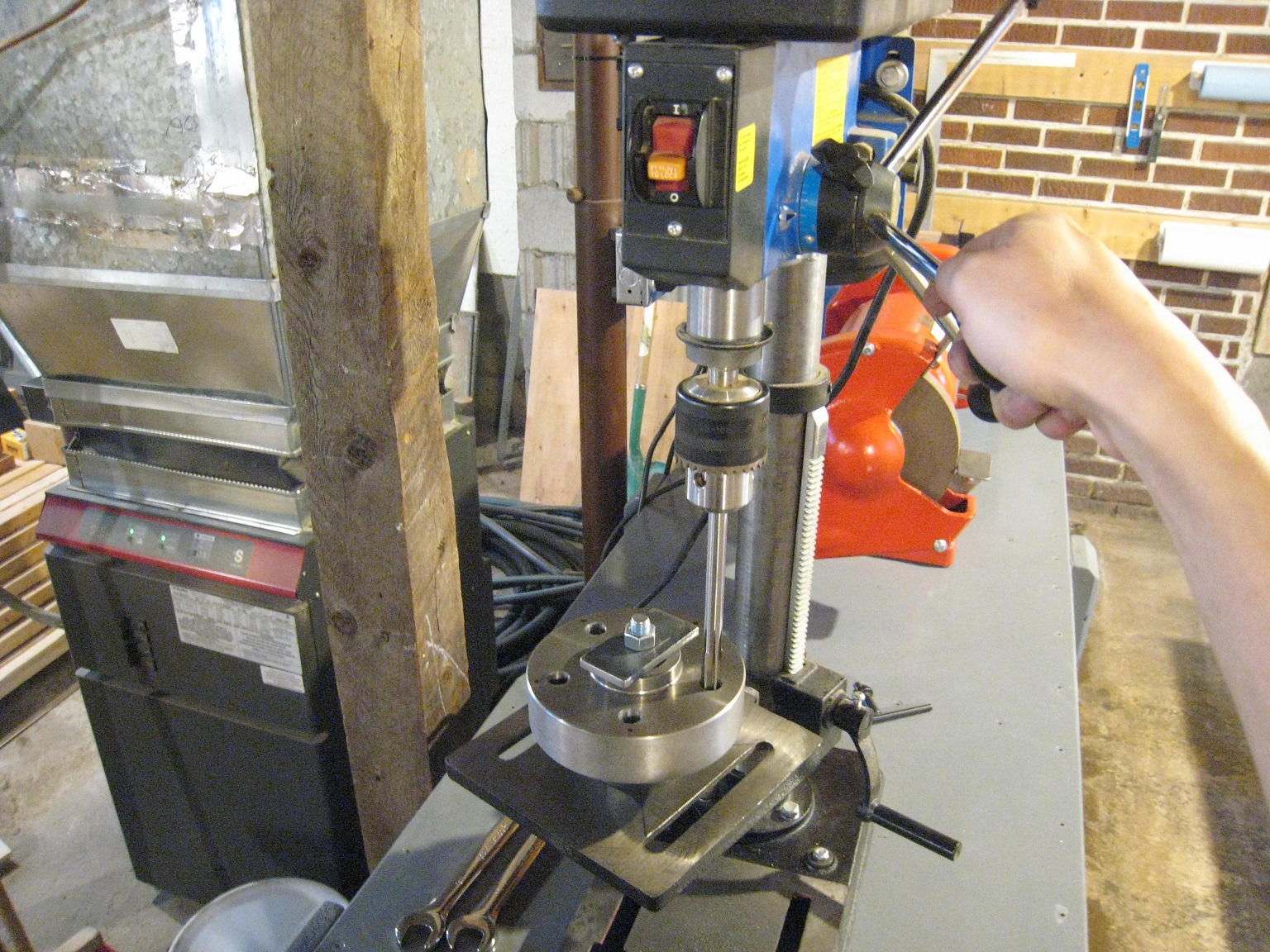
Backside of hubs painted with POR-15, and brake rotor register built up with Permatex Steel Weld epoxy:
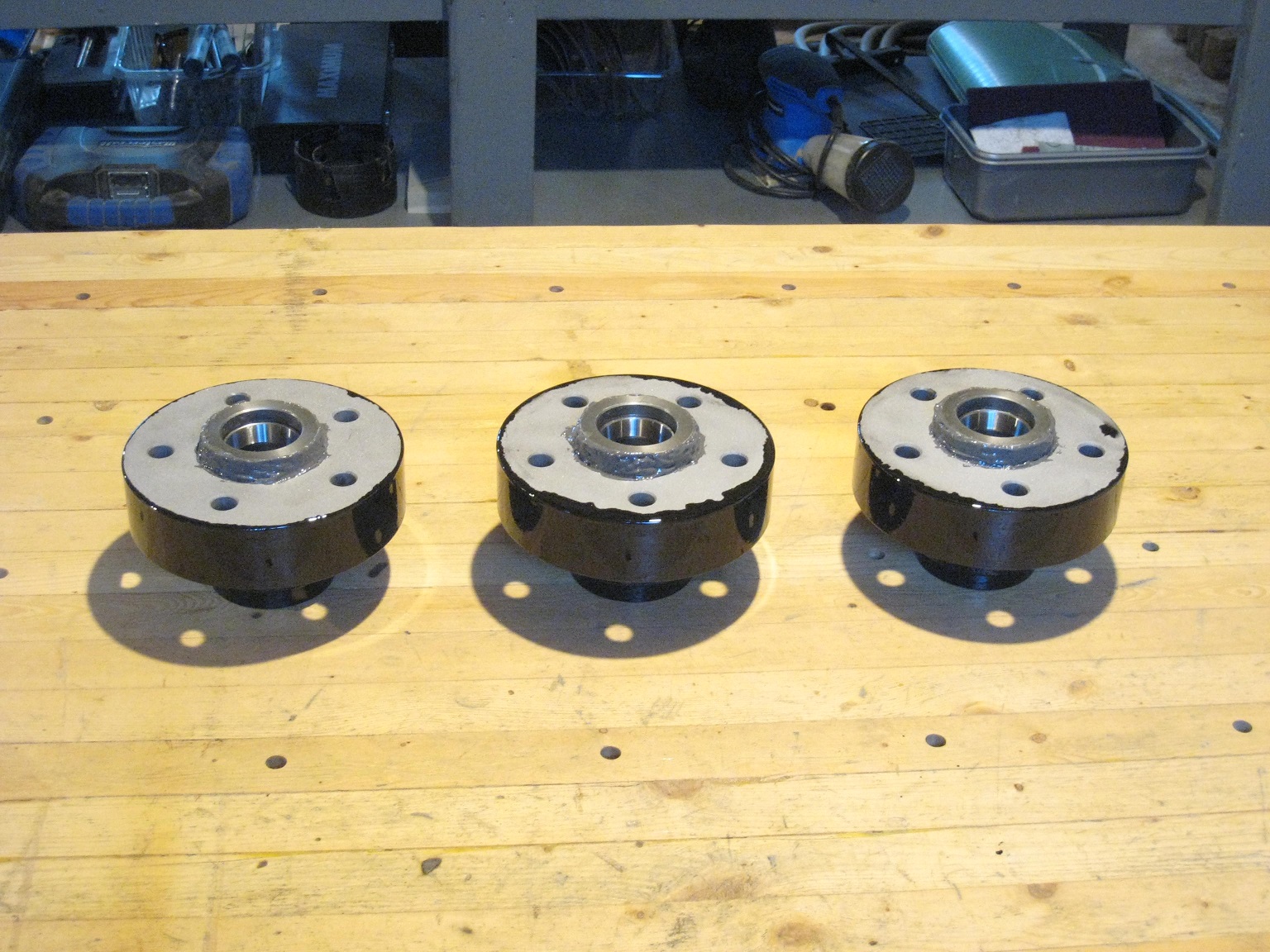
I made a tool to support the hub while pressing in the lug studs. The tool has a 12 mm hole to help keep the stud aligned.
|
|
|
pmbrunelle
|
MAR 25, 08:30 PM
|
|
I finished the modified rotor/hubs.
With my knuckle between centres setup, I ended up with about 0.001" of runout. Good enough.
|
|
|
zkhennings
|
MAR 28, 12:53 PM
|
|
Nice work! Curious how well that JB weld will hold up, it should not see any stress, but might take a beating removing and installing wheels.
|
|
|
pmbrunelle
|
MAR 28, 06:09 PM
|
|
Some hubcentric rings for wheels are made of plastic 
In this case, I'm only using the Permatex Steel Weld to centre the brake rotor.
The wheel has a large centre bore (alignment is via the 60° conical lug nuts), so the wheel won't rub on the epoxy during installation/removal.
|
|
|
zkhennings
|
APR 02, 02:27 PM
|
|
Did not realize it was just for the rotors, I wouldn't expect any issues then. I was speaking more to the ability of the metal reinforced epoxy to chip because it is pretty hard, almost like a ceramic, and I have had it chip/crack on me before. The plastic rings are soft enough they will not chip, but they are a pain as eventually they don't fit as snug, I have had to glue mine into my wheels after a few years where they used to stay installed from friction. But removing/installing rotors is much more gentle than removing/installing wheels.
|
|

 |
|