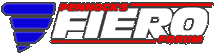

 |
Blooze Own: An F355 Six Speed N* Build Thread (Page 88/126) |
|
kennn
|
DEC 21, 11:21 AM
|
|
Hey Blooze,
This may be a type of bump stop that is located on the shaft of the shock. I didn't confer with QA1.
<http://www.qa1.net/qa1_motorsports/catalog/product/gallery/id/7021/image/77/>
Ken
edit: Or this one <http://www.qa1.net/qa1_motorsports/catalog/product/gallery/image/1201/id/7021/>[This message has been edited by kennn (edited 12-21-2013).]
|
|
|
motoracer838
|
DEC 21, 12:50 PM
|
|
nevermind, I was wrong.
Joe[This message has been edited by motoracer838 (edited 12-21-2013).]
|
|
|
Bloozberry
|
DEC 21, 10:16 PM
|
|
OK so this post might look like déja-vu but it's kind of like one of those games where you have to spot the differences. Following Will's advice, I've revised the ratio of the bell crank from 1:1 to 1:0.88 by reducing the length of the arm that the coil over attaches to by 13mm (from 107 mm to 94 mm) so now it looks like this:

By keeping the same 14.5" shock length at ride height as before, the simple change in the bell crank allows the wheel to travel the full 3" of jounce while compressing the coil over by only 2.625". This means that when the wheel reaches the end of its upward travel the shock absorber will still have 0.25" of travel left (ie it won't bottom out and destroy the shock). Conversely, in rebound when the wheel travels to its rebound bump stop 2.5" downward, the coil over will extend by only 2.2" leaving a buffer zone of another 0.25" at the opposite end of the shock's travel.
Here are the new drawings of the coil over at ride height and at the two extremes. Notice how the new configuration increases the length of the spring at full jounce over the previous design thereby reducing the likelihood of the coils binding. A similar improvement also occurs in full rebound where the spring remains compressed by a little more than 0.4" making sure it won't flop around even in the worst scenario.

Shortening the shock absorber arm on the bell crank had the potential to worsen the interference between the spring hat and the crank especially at full rebound so the last thing to check were the clearances with the new bell crank. Again, everything checked out fine:

Two other benefits of having modified the bell crank are that it lowers the coil over in the engine bay making a bit more room under the deck lid for future adjustments, and with it being lower, the sight lines to them from the open deck lid improve as well. These things are way too good looking to be hidden!
|
|
|
Bloozberry
|
DEC 25, 08:45 PM
|
|
The bell crank dimensions finally worked out, I could now complete the design of the upper mount for the bell crank, as well as the forward stationary mount for the coil-over shock. Again, the best way to describe what I propose is to simply post the drawing and point out a few of the most important features, so here is the rear view:
_Notes.jpg)
Of the three different views I'll be posting, the rear view is the most revealing. The upper and lower crank mounts (A & B) are the most clear in this one... they're just capped off 2" x 3" x 1/8" wall rectangular tubes. The upper mount drops down from the new upper frame rail stiffener (C) that I added to the chassis a few posts ago. There are a few things to note about this area so I've broken them down the following sub-paragraphs:
1. you can clearly see how the original cross section of the upper frame rail has been modified. I've left a barely visible outline of the part that was removed (D) just to show what it used to look like. I've also drawn an outline of the wheel and tire at full jounce (76 mm) to show why it was necessary to notch the bottom of the rail;
2. the stiffener (C) will serve as the main anchor point for the upper bell crank mount (A). The top of the mount will also be welded to the underside of what's left of the old strut tower. That portion of the strut tower is made up of two heavy gauge steel plates welded together. This area will get a further boost in strength when I eventually drop a steel C-pillar down from the roof to the top front corner of the strut tower. The previous owner had already done something similar with some round tubing however it isn't properly anchored to the roof;
3. the rear view also shows how the bell crank (E) and coil over (F) clear the mounts side to side and from the bottom. I had to square off the top corner of the lower crank mount (B) since the aft end of the coil-over angles downward by about 20 mm in full rebound and would otherwise have contacted the top of the mount;
4. to tighten the bell crank bearing bolt, the bell crank mounts will have an angled access hole (G) machined in one wall large enough to get a socket wrench on the nut and bolt;
5. the angle of the bell crank and pushrod wasn't just arbitrarily chosen. Notice how a line (H) drawn though the center of the crank down through the lower end of the push rod lines up perfectly with the outboard lateral link pivot. Having these parts line up this way ensures a 1:1 ratio between the wheel movement and the pushrod movement... i.e. 1" upward movement of the wheel translates into 1" upward movement of the pushrod (at least initially at ride height). This ratio can be whatever you want it to be, but the longer the movement of the pushrod, the more easily fine adjustments can be made to damp the spring. (Of course I reduced the ratio of the motion actually transmitted to the shock with the non-equal length arms on the bell crank); and
6. lastly, if you recall from earlier drawings, I stole an idea from Yarmouth Fiero by adding an upper cross car brace (I) under the rear window. The plan is to use that brace to mount the stationary end of the shocks, the engine torque struts, and the deck lid hinges. The change I made to this area from earlier drawings is that I now plan to run the drop down supports (J) vertically to the lower frame rail rather than angling them outwards at the top to meet up where the cross car brace meets the upper frame rail. Making them vertical not only makes them easier to weld and cut, but also very conveniently makes them line up directly with the stationary coil-over mount, giving the area better strength and rigidity to react the spring's forces.
Tired of reading? You should try typing this stuff out. OK, on to the side view to see what gems might be hiding there:
.jpg)
In this view you get a better idea how the vertical supports for the cross car brace (fuchsia) are anchored to the lower frame rail, and despite being mostly hidden by the upper frame rail, you can also see how the stationary coil-over mounts project backwards to meet up with the shock.
You can also see how the coil-over is at the same height as the upper frame rail (well-below the deck lid). This keeps the forces exerted on the cross car brace in the same plane (in the side view) as the main structures that react them. It just means that the cross car brace will be under a simple bending force rather than a compound bending and torsional force.
Two last tidbits from this view: if you look closely, you'll see the large hole in the upper bell crank mount to provide access to the crank bearing bolt with a socket wrench I mentioned earlier and; for those who haven't fallen asleep yet, you'll notice I've pencilled in an additional pushrod off the crank that leads to a sway bar (brown). I got the idea for a rear mounted bar off the bell crank when I saw this particular photo online:

For now it's just a concept since I may or may not use a sway bar, but interestingly enough, it appears the stock '88 rear sway bar would fit in that space like a well made glove.
Lastly, the top view is always the most obscured view since everything is layered very much vertically. The view does give a bit of insight into how some of the pieces fit though:
.jpg)
Here, the stationary coil-over mounts are much more visible, as is the shape of the left-over strut tower (light green). I've mentioned it before, but I left the top piece of the strut tower in a triangular shape to act as a gusset between the upper frame rail and the old strut tower brace that's integral with the trunk wall. If I do indeed use a sway bar set up like I've pictured here, I might need to replace the old strut tower brace with a different design so as not to interfere with the movement of the sway bar arms.
One final thing to note about the potential use of a sway bar connected to the bell crank is that it would place some more complicated loads on the bell crank bearings due to the slight offset of having the sway bar pushrod mounted to the side of the crank. Some more research would be needed if I decided to go this way, but I'm not going to study it at this point.
So there you have it. This pretty much completes the design phase of the rear SLA suspension. Please don't be shy if you have any questions, concerns, or I didn't explain something clearly.
|
|
|
Yarmouth Fiero
|
DEC 25, 09:15 PM
|
|
Looks really good Blooz. It's certainly going to be an interesting feature when you look in the engine bay. Is there any room to add gussets to the lower end of part B and the lower frame rail?
What is the red car in the picture you used? Looks like their bell crank has a much large ratio.... maybe 1.5 : 1.
Merry Christmas to you and your much better half from the Oakleys.
|
|
|
Bloozberry
|
DEC 26, 08:10 AM
|
|
There is a fair bit of room for gussets if needed, though given the stoutness of the lower mount and the direction of the forces involved, I think it'll be OK.
The bell crank on the red car in the photo doesn't make a lot of sense to me too. The shock length looks too short and the spring coils too close for there to be much jounce travel, and the bell crank ratio certainly doesn't make things better. It's a race car though so I doubt it sees anything but smooth asphalt. I didn't pay much attention to the actual article but if I recall correctly the car was one of those American university Formula SAE cars. As I recall, the article was written by an FSAE technical judge who wanted to point out some of the areas where past teams had lost points. In this example he was pointing out how the bell crank pushrod and shock were held to the crank in single shear.
Best of the season to you and your family too.
|
|
|
Bloozberry
|
JAN 01, 10:02 PM
|
|
With the holiday-hoopla winding down, I found some time to finish modifying the passenger rear upper frame rail with the tire notch and reinforcement. I also managed to get a few parts in the mail for the bell crank from Summit Racing. These are the SG105 stainless spacers made by QA1 that are 5/16" thick and have a 5/8" bore for the crank fulcrum bolt:

Santa also delivered the crank bearings too. These are the FK S10 spherical bearings that I plan to use (two per crank). Notice they have a predrilled lubrication hole and groove. I'll have to update the crank hub design with zerk fittings:

I also found some time today to start fabricating the parts for the first bell crank. The pieces below are the main body of one crank and are cut out of 3/16" thick steel plate. The smaller pieces will be overlapped onto the larger pieces when welded, making the spacing between them 1.0" while the spacing between the main body halves will be 5/8". The drawing a couple posts up shows how they're overlapped. I haven't drilled out the lightening hole in the center yet because I want to wait until the parts are welded to the crank hub to minimize warpage.

Next step is getting more 3/16" plate to make the other crank, and popping by the machine shop to see about getting some DOM tubing machined to accept the bearings and a snap ring. Hopefully that won't cost too much.
|
|
|
Bloozberry
|
JAN 09, 07:55 PM
|
|
While I am waiting for an opportunity to use a friend's lathe for the bell crank bearing housings, I thought I'd get around to something I've been meaning to do for a while: create an index for the thread. For convenience, I've edited my very first post on page 1 with a guide to navigating the past 22 pages.
I should get around to some real progress by tomorrow.
|
|
|
doublec4
|
JAN 09, 11:56 PM
|
|
Still watching this build! Has to be the most well thought out and methodical builds I've ever seen.
May I ask where you bought those spherical bearings?
|
|
|
Insky
|
JAN 11, 05:53 PM
|
|
I'm interested in doing a similar project, and this thread has been a great resource. One of the main things that may prevent me from pursuing a project like this is liability. Has anyone done any in depth research about what kind of liability a builder may have if they eventually sell the project?
This project has the benefit of being reviewed/approved by a PE, but there isn't a requirement, that I am aware of, in Indiana.
|
|

 |
|