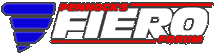

 |
$130 Headers Without Cutting the Trunk (Page 1/2) |
|
Stricken
|
OCT 24, 11:02 PM
|
|
|
|
Dennis LaGrua
|
OCT 25, 07:50 AM
|
|
Love those headers. Incredible job of exhaust plumbing. It took quite a bit of measurement as all the bends are now in the right places. While I mig weld myself I could not have done as well. I would have probably gone the easier route and used mandrel bends on the rear side. ------------------ " THE BLACK PARALYZER" -87GT 3800SC Series III engine, custom ZZP /Frozen Boost Intercooler setup, 3.4" Pulley, Northstar TB, LS1 MAF, 3" Spintech/Hedman Exhaust, P-log Manifold, Autolite 104's, MSD wires, Custom CAI, 4T65eHD w. custom axles, Champion Radiator, S10 Brake Booster, HP Tuners VCM Suite. "THE COLUSSUS" 87GT - ALL OUT 3.4L Turbocharged engine, Garrett Hybrid Turbo, MSD ign., modified TH125H " ON THE LOOSE WITHOUT THE JUICE "
|
|
|
fieroguru
|
OCT 25, 01:29 PM
|
|
|
|
theogre
|
OCT 25, 02:39 PM
|
|
While seems good because can weld thin tube w/o a leak etc. because Most people can't do the same... Sadly, might not last long.
Engine and exhaust will move quite a lot and load any weak section(s) causing cracks at minimum. Highlights: Even tho muffler has springs/hangers to mount, muffler and pipes are heavy enough to hammer the header and the short "down pipe." Engine itself and exhaust "grows" and "shrinks" as it runs then shuts off. Exhaust insulation tape can add to this problem as keep heat trapped to "overheat" the pipe.
Heal cycling and motion is why header kit came w/ flex part(s). Is why many OE Doughnut joints have "spring bolts" to allow movement and rotation as engine moves on 3 planes.
"Dog bones" and engine/trans mounts try to limit engine moving but doesn't prevent exhaust hammering as you go, stop, hit pot holes, backup and hit the exhaust, and so on. (Is likely why GM spend money to add an extra joint and "hanger" in the down pipe for 88 Fiero L4 to stop breaking exhaust manifold. Upper section is bolted to the tran's. Extra joint is in 180° turn for the cat.)------------------ Dr. Ian Malcolm: Yeah, but your scientists were so preoccupied with whether or not they could, they didn't stop to think if they should. (Jurassic Park)
The Ogre's Fiero Cave
|
|
|
pmbrunelle
|
OCT 25, 02:39 PM
|
|
That's much nicer than having the exhaust point straight back!
|
|
|
pmbrunelle
|
OCT 25, 02:53 PM
|
|
quote | Originally posted by theogre: Even tho muffler has springs/hangers to mount, muffler and pipes are heavy enough to hammer the header and the short "down pipe."
|
|
The ideal scenario where a flex pipe is not feasible would be to have the exhaust hanger supports be fixed to the powertrain, and not the spaceframe/cradle. This way, as the powertrain rocks, the exhaust hangers move in unison, without imparting stress on the exhaust. You just have to check for adequate exhaust tip to bumper clearance on launch.
I remember seeing fieroguru doing exactly this in one of his project threads. He had engine/trans-mounted struts going out to the back to help support the exhaust pipes. Guru, care to share?
In my Fiero project I did it the way theogre mentions, with the flex pipe, and the exhaust supported by the cradle:
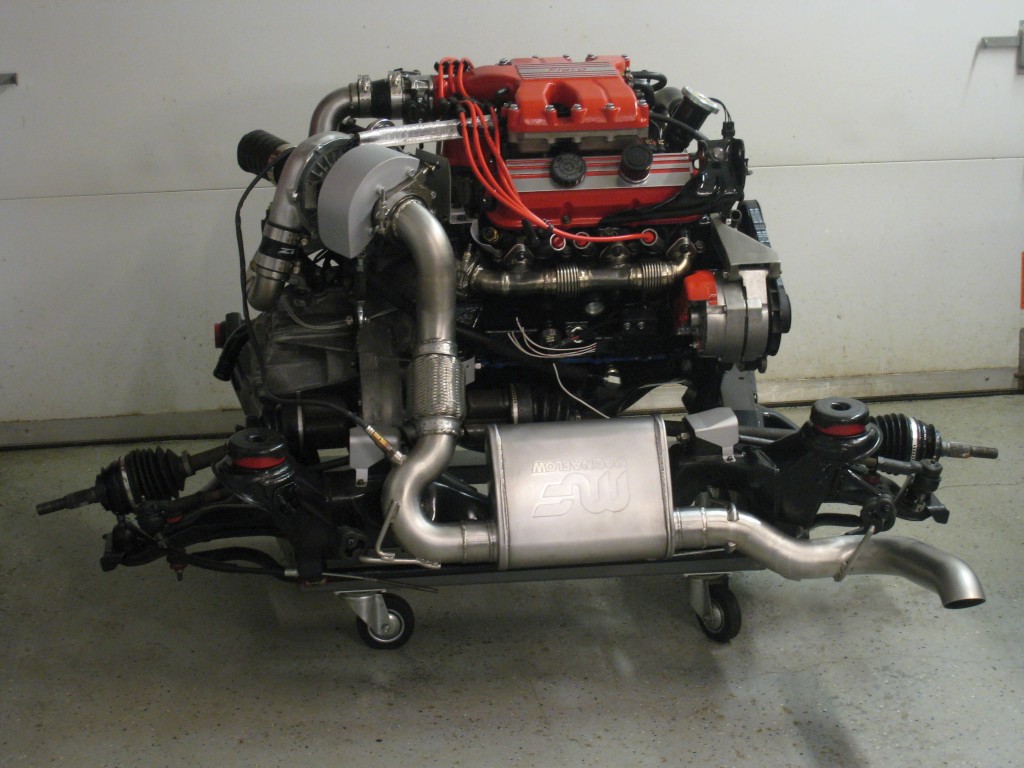
Both ways are valid, but flex pipes do eventually die.[This message has been edited by pmbrunelle (edited 10-25-2020).]
|
|
|
theogre
|
OCT 25, 03:05 PM
|
|
quote | Originally posted by pmbrunelle: Both ways are valid, but flex pipes do eventually die. |
|
Maybe but when that happens you hope to only need to fix the flex. Most OE installed flex last for many years, even several decades, vs. DIY installed flex is anyone's guess how long it will last.
|
|
|
pmbrunelle
|
OCT 25, 03:21 PM
|
|
I have seen flex pipes die to 10-15 year old cars.
On OP's exhaust, there is no room to add a flex section, so the fieroguru method would be recommended instead.
|
|
|
fieroguru
|
OCT 25, 07:32 PM
|
|
quote | Originally posted by pmbrunelle: The ideal scenario where a flex pipe is not feasible would be to have the exhaust hanger supports be fixed to the powertrain, and not the spaceframe/cradle. This way, as the powertrain rocks, the exhaust hangers move in unison, without imparting stress on the exhaust. You just have to check for adequate exhaust tip to bumper clearance on launch.
I remember seeing fieroguru doing exactly this in one of his project threads. He had engine/trans-mounted struts going out to the back to help support the exhaust pipes. Guru, care to share?
|
|
Worked great! I will be doing something similar with the new exhaust post turbo.
|
|
|
Stricken
|
OCT 25, 10:15 PM
|
|
I'd credit cracking more to the cheap ChinaBay stainless, but I'm really not worried. The muffler is supported on soft mounts.
For $130, it's worth using as a jig to make them from mild or 409.
|
|

 |
|