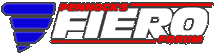

 |
What gauge for battery wires? (Page 2/2) |
|
theogre
|
JUL 17, 12:01 PM
|
|
quote | Originally posted by Dennis LaGrua: Many OEM electrical connections on the Fiero were made with solder and they don't come loose. |
|
Huh? GM has Not used solder for most wire joints on any cars for 40 to 50+ years. All Weather Pack, Metripak, Packard (Marked w/ PED on the plastic shells) and other wire ends and splices are crimped w/ so much force the wires and ends "cold weld" the parts together and very hard to remove w/o cutting. Big cables like battery ends are often hydraulically crimped on the cables w/ 10 to 20 Tons of pressure. Often the Wires will actually flow under OEM crimping force to close voids to prevent corrosion and to get the best connection.
Only soldering is used to make ECM, all color of dingy thingy, gen2 HL module, and retailed assemblies. GM and others often tell "you" to crimp then solder weather pack etc ends because you can't crimp with most crimp tools well enough to not have big problem latter. Example the newer metripak pig tail for new style ECT often have directions to do just that because crap hand crimping often causes ECM problems.
Note that Real GM side terminal ends have "locking ears" so terminal won't vibrate or rotate loose unlike lead ends etc that will come loose easy when the bolts are torque correctly meaning 17 N·m (13 lb. ft.) per any FSM in the battery section.
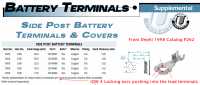 | CLICK FOR FULL SIZE |
Is why they sell the short "battery wrench" to limit force by users. Most damage to the battery is done by twits that use way too much torque, that think is easy to make good cables and more so w/ side terminal batteries that ID10ts rips the nut/treads right out of the lead.
The only thing I do w/ GM and other OEM battery cables is to pull off loose plastic covers and coat the metal w/ silicon or brake grease to keep polluted water and acid off then put the cover back on. Most times I don't pull off the top terminals just to grease them and use "Q-tip" etc to access tight places. Been doing that for decades and works better then most other methods including most sold by auto parts and other stores.
|
|
|
Synthesis
|
JUL 17, 01:17 PM
|
|
When I was building my battery cable kits, I only used solder on the wire that connected the power block to the starter. Testing the cabling with a soldered lug resulted in cracks in the joint.
The front battery relocation can easily work with QUALITY 4ga wire. Most cables you find in the parts stores are not Cross-linked polyethylene coated 99% OFC Copper. They tend to be slightly smaller than true 4g with a vinyl coating and a poor crimp connector. If you intend to build cables, I'd suggest you source forged terminals without a brazed splice in the cable insert, and do not use solder for high-amperage and large gauge cables.
|
|
|
Dennis LaGrua
|
JUL 18, 04:39 AM
|
|
quote | Originally posted by Synthesis:
When I was building my battery cable kits, I only used solder on the wire that connected the power block to the starter. Testing the cabling with a soldered lug resulted in cracks in the joint.
The front battery relocation can easily work with QUALITY 4ga wire. Most cables you find in the parts stores are not Cross-linked polyethylene coated 99% OFC Copper. They tend to be slightly smaller than true 4g with a vinyl coating and a poor crimp connector. If you intend to build cables, I'd suggest you source forged terminals without a brazed splice in the cable insert, and do not use solder for high-amperage and large gauge cables.
|
|
Strange. I've had soldered lugs on my 3800SC swap for 7 years and they are still firmly in place. With my soldered lugs there is no joint. The entire cavity of the lug is filled with rosin core solder. However, I do slightly crimp the ends using a punch and hammer lug and the wire end is covered with solder. In other words I fill the entire lug cavity with rosin core solder. ------------------ " THE BLACK PARALYZER" -87GT 3800SC Series III engine, custom ZZP /Frozen Boost Intercooler setup, 3.4" Pulley, Northstar TB, LS1 MAF, 3" Spintech/Hedman Exhaust, P-log Manifold, Autolite 104's, MSD wires, Custom CAI, 4T65eHD w. custom axles, Champion Radiator, S10 Brake Booster, HP Tuners VCM Suite. "THE COLUSSUS" 87GT - ALL OUT 3.4L Turbocharged engine, Garrett Hybrid Turbo, MSD ign., modified TH125H " ON THE LOOSE WITHOUT THE JUICE "
|
|
|
theogre
|
JUL 18, 12:20 PM
|
|
Guys if you ever read how to use solder... First Rule is parts Must have a Good Mechanical connection Before you solder anything Because Solder has Never be made to take Mechanical Loads. For wire to wire or wire to terminal, you must splice etc to close any gap before you solder. IOW When you parts fail apart before you solder then the joint will crack. That is Just a matter of time.
Example: "Western Union splice" works without soldering. Soldering adds some strength but is mostly just to seal the joint. If you use it on Stranded wire solder keeps strands in place too but the wire in a joint still takes most all Mechanical Loads.
Is why If you actually read any FSM and other books for cars,,, You crimp a end then Solder. Not just solder the end on. But many watch YT and other BS videos made by morons w/o a clue. So many problems to list here but isn't only most fail to follow the First Rule of soldering.
That rule even apply to most small parts on circuit boards. Just read Chime Unit in my Cave for defects. Many problem are holes on boards that fail to have proper hole to fit a part as shown in that page and solder gaps are too big etc.
Is very common for Surface Mount parts failing for crack solder. Worse w/ RoHS lead free solder that's often very brittle. Manufacturing realize only on solder to keep parts together and often fails in big ways. Is Why there are so many YT videos that show DIY reflowing of PS, PC Video cards, etc. Some might work but those boards often fail again.
Even for Plumbing work... Soldering copper need a very small gap and big surface to even hope the joint will last Plus the pipes need to have Mechanical Support too or pipe hammering, heat cycling and building vibration can crack any or all joints. Lead free solder have problems here too.
quote | Originally posted by Dennis LaGrua: Strange. I've had soldered lugs on my 3800SC swap for 7 years and they are still firmly in place. With my soldered lugs there is no joint. The entire cavity of the lug is filled with rosin core solder. However, I do slightly crimp the ends using a punch and hammer lug and the wire end is covered with solder. In other words I fill the entire lug cavity with rosin core solder. |
|
Sorry but If you cut those ends apart and look... many times flux core solder doesn't flux inner core of big wires/cables and solder doesn't flow there. If you use liquid flux on a wire before you solder will often get a much better results.
Any voids/crack in a solder joint is bad and same bad as crap hand crimping anything. That will allow water etc to attach the joint inside out and you often won't see this happening until the joint is completely rotten.
|
|
|
justin87
|
JUL 18, 04:27 PM
|
|
quote | Originally posted by theogre:
Guys if you ever read how to use solder... First Rule is parts Must have a Good Mechanical connection Before you solder anything Because Solder has Never be made to take Mechanical Loads. For wire to wire or wire to terminal, you must splice etc to close any gap before you solder. IOW When you parts fail apart before you solder then the joint will crack. That is Just a matter of time.
Example: "Western Union splice" works without soldering. Soldering adds some strength but is mostly just to seal the joint. If you use it on Stranded wire solder keeps strands in place too but the wire in a joint still takes most all Mechanical Loads.
Is why If you actually read any FSM and other books for cars,,, You crimp a end then Solder. Not just solder the end on. But many watch YT and other BS videos made by morons w/o a clue. So many problems to list here but isn't only most fail to follow the First Rule of soldering.
That rule even apply to most small parts on circuit boards. Just read Chime Unit in my Cave for defects. Many problem are holes on boards that fail to have proper hole to fit a part as shown in that page and solder gaps are too big etc.
Is very common for Surface Mount parts failing for crack solder. Worse w/ RoHS lead free solder that's often very brittle. Manufacturing realize only on solder to keep parts together and often fails in big ways. Is Why there are so many YT videos that show DIY reflowing of PS, PC Video cards, etc. Some might work but those boards often fail again.
Even for Plumbing work... Soldering copper need a very small gap and big surface to even hope the joint will last Plus the pipes need to have Mechanical Support too or pipe hammering, heat cycling and building vibration can crack any or all joints. Lead free solder have problems here too.
[QUOTE]Originally posted by Dennis LaGrua: Strange. I've had soldered lugs on my 3800SC swap for 7 years and they are still firmly in place. With my soldered lugs there is no joint. The entire cavity of the lug is filled with rosin core solder. However, I do slightly crimp the ends using a punch and hammer lug and the wire end is covered with solder. In other words I fill the entire lug cavity with rosin core solder. |
|
Sorry but If you cut those ends apart and look... many times flux core solder doesn't flux inner core of big wires/cables and solder doesn't flow there. If you use liquid flux on a wire before you solder will often get a much better results.
Any voids/crack in a solder joint is bad and same bad as crap hand crimping anything. That will allow water etc to attach the joint inside out and you often won't see this happening until the joint is completely rotten.[/QUOTE]
Maybe i'm missing something, but I always thought that solder, while a conductor, was usually used to hold something in place or to make a more secure connection (but there had to be a connection first), i/e twist the wires together THEN solder, where the solder becomes secondary and in-addition-to rather than in place as the primary connection. Please forgive my ignorance, as part of this project for me IS learning and I am by no means an expert; but my real question is... If I were to do as described with the lug, in that I took 4 ga wire, stripped it back just enough, heated the lug, placed the wire and solder in it to make the connection. Ive seen multiple youtube videos of people doing exactly that but there seems to be some argument that it is incorrect.... Why? The comments section usually say something like "it will fail!" but with no reasoning or anything backing it up followed by others ancedotally saying they did the same thing and it works just fine.
For reference, this is one video showing the process: https://www.youtube.com/watch?v=x4MapRlYG7A
|
|
|
Larryinkc
|
JUL 18, 05:52 PM
|
|
|
|
theogre
|
JUL 18, 07:37 PM
|
|
Those do work but coat them w/ silicon/brake grease to keep out "water" after installing them then heatshrink. Or try weather resistant heatshrink. That has "glue" that melts to seal whatever in it. Main problem w/ them is bigger then OEM ring ends and often have a hard time on anchor bolts in tight places.
|
|
|
theogre
|
JUL 18, 10:07 PM
|
|
quote | Originally posted by justin87: Maybe i'm missing something, but I always thought that solder, while a conductor, was usually used to hold something in place or to make a more secure connection (but there had to be a connection first), i/e twist the wires together THEN solder, where the solder becomes secondary and in-addition-to rather than in place as the primary connection. Please forgive my ignorance, as part of this project for me IS learning and I am by no means an expert; but my real question is... If I were to do as described with the lug, in that I took 4 ga wire, stripped it back just enough, heated the lug, placed the wire and solder in it to make the connection. Ive seen multiple youtube videos of people doing exactly that but there seems to be some argument that it is incorrect.... Why? The comments section usually say something like "it will fail!" but with no reasoning or anything backing it up followed by others ancedotally saying they did the same thing and it works just fine.
For reference, this is one video showing the process: https://www.youtube.com/watch?v=x4MapRlYG7A |
|
Everyone saying that method in the video will fail is correct but most don't bother why because most of YT including the video maker won't read or just flame them for not buying their garbage. So Why? Say Assuming he used flux core... I'll say that because as solder melt coats part of the side in the hole. Small amount of solder use does not have enough flux for size of joint to start. Wire has no flux and even if solder was flux core that flux was gone before wire went in. Also Wire is cold and most solder there won't flow into the wire. So you have a "Cold Joint" or worse that will fail just for that reason alone. And that's ignoring standard heatshrink will allow water to attack the weak joint.
For big joints, Similar to plumbing, you coat both parts w/ flux then solder. Paste flux is ok mainly for solid big parts but small amount of Liquid flux will coat every strand of that wire w/o bothering the wire. And I mean one small drop or two of good quality liquid flux is all you need for most jobs. In fact proper flux can wick far under the insulation and if not careful the excess solder will follow that. They make tools and chemicals specifically to prevent that but most are for small parts/wires. (Google solder anti wicking tweezers)
Side Note: Many Plumber don't use Acid Flux. Why? Leftover Acid flux inside of copper pipes can cause pipe failures months to years later. More so w/ thinner copper tubes. (Go to HD etc and look at 10' ridged copper tubes in plumbing aisle. The one that's lighter and often has dents has much thinner walls and cheap/dumb people love them.)
Another big problem is when you see a soldering iron or gun and the joint is too big. Like 25w or less iron to heat 14g and bigger wire. Wire will heatsink the joint and often result in a "cold joint" at best. May look ok and even stay put for some time but have big problems hidden by looking good. If the joint eventually does get hot enough to flow right, you often melt the insulation and make a big mess.
People saying most crap soldering videos are good have no real solder job experience and should ignore them. Only a few times you find videos that are made by real experts... sometime posted by the owners or stolen and posted and owner doesn't bother for whatever reason. Example: https://www.youtube.com/watch?v=xpiyB7ZM3vg video owned by BEST Inc. @ https://www.solder.net/[This message has been edited by theogre (edited 07-18-2019).]
|
|
|
Dennis LaGrua
|
JUL 19, 08:47 PM
|
|
Years back battery terminals were molded of 100% solid lead cast around the battery cable. They held up fine without a mechanical connection. I'll keep checking my cables but after 7 years the wires are still firmly in place. ------------------ " THE BLACK PARALYZER" -87GT 3800SC Series III engine, custom ZZP /Frozen Boost Intercooler setup, 3.4" Pulley, Northstar TB, LS1 MAF, 3" Spintech/Hedman Exhaust, P-log Manifold, Autolite 104's, MSD wires, Custom CAI, 4T65eHD w. custom axles, Champion Radiator, S10 Brake Booster, HP Tuners VCM Suite. "THE COLUSSUS" 87GT - ALL OUT 3.4L Turbocharged engine, Garrett Hybrid Turbo, MSD ign., modified TH125H " ON THE LOOSE WITHOUT THE JUICE "
|
|

 |
|